Van brownfieldfabriek tot hoogkwalitatieve EV-productiefaciliteit
Met de Vlaming Vic Daenen aan het roer
We staan aan de wieg van de elektrische Explorer en Capri van Ford. Meer bepaald in het Ford Cologne Electric Vehicle Center, gevestigd in de oude fabriek waarin Ford al sinds 1930 auto’s bouwt. Een deel van die site is intussen omgevormd tot een state-of-the-art productie-eenheid waarin jaarlijks 250.000 elektrische personenwagens geassembleerd kunnen worden. We worden rondgeleid en oordeelkundig geïnformeerd door de Vlaming Vic Daenen. Hij was de laatste fabrieksdirecteur bij Ford Genk en voert hier al tien jaar het commando. De welbespraakte Limburger stond dus ook aan het roer toen deze historische Ford-fabriek in nauwelijks enkele maanden tijd omgevormd diende te worden tot een hoogkwalitatieve EV-productiefaciliteit.
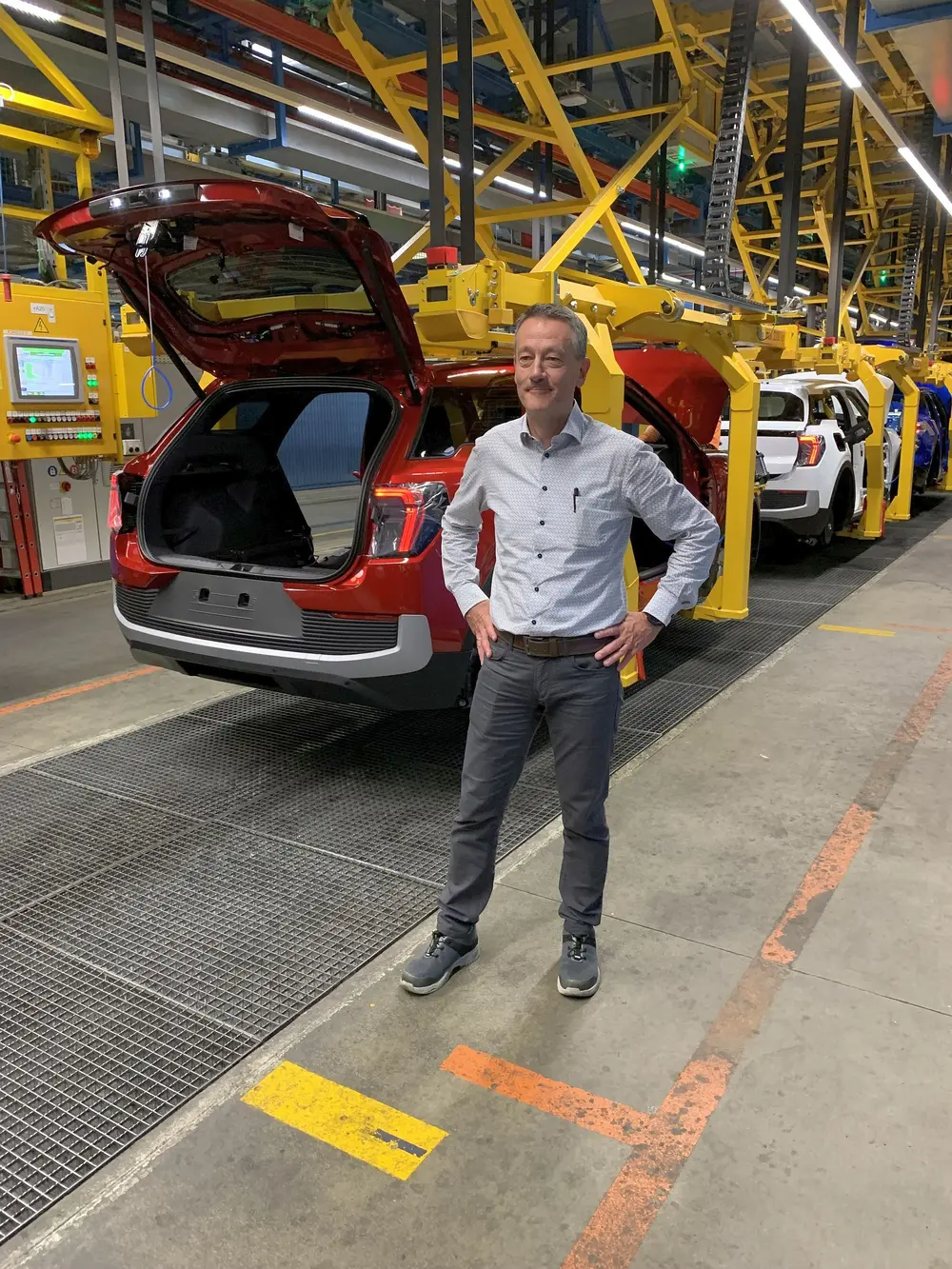
Het Ford Cologne Electric Vehicle Center vormt het recentste hoofdstuk in de geschiedenis van een Ford-site waar sinds 1930 onder meer de Model A, Taunus, Capri, Granada en (tot juni 2023) Fiesta van de assemblagelijn werden gereden. Het was na de productiestop van de Fiesta – en met het oog op de naderende productie van de Ford e-Explorer en e-Capri – dat de Ford-fabrieken in Keulen een ware metamorfose moesten ondergaan.
Compleet nieuwe productielijn
Om in de bestaande fabrieksgebouwen (brownfield) de oude ICE-assemblage (modellen met verbrandingsmotor) te kunnen transformeren naar BEV-productie (batterijgedreven modellen) was sprake van een investering van € 2 miljard. De investering op het 125 hectare grote fabrieksterrein heeft onder meer geleid tot een efficiënt toegeleverde en compleet nieuwe productielijn, batterijassemblage, state-of-the-art tooling en (niet in het minst) nog verder doorgedreven automatisering. Ford Keulen – of voortaan Ford Cologne Electric Vehicle Center genaamd – is daarmee de eerste dergelijke EV-productiefaciliteit van Ford in Europa. Dit met een jaarlijkse productiecapaciteit van 250.000 elektrische personenwagens.
Strategische allianties
Ford kan nu – naast de Mustang Mach-E, de E-Transit en de F-150 Lightning – zijn wereldwijde EV-modelaanbod uitbreiden met twee in Keulen gebouwde – en voor de Europese markt niet onbelangrijke – nieuwkomers: de elektrische Explorer, een middelgrote SUV, en een op deze Explorer gebaseerde sportieve crossover, vernoemd naar de uit de zestiger en zeventiger jaren van de vorige eeuw legendarische Ford Capri.
Belangrijk om te weten: net zoals Ford en Volkswagen op het gebied van bestelwagens een strategische alliantie voor kosteneffectieve voertuigontwikkeling hebben, zijn ze voor de productie van de Explorer/Capri eveneens in zee gegaan met VW. Zoals we eerder al schreven, heeft Ford voor de in Keulen geassembleerde Explorer en Capri het Volkswagen-MEB-platform van de VW ID.4 onder licentie genomen.
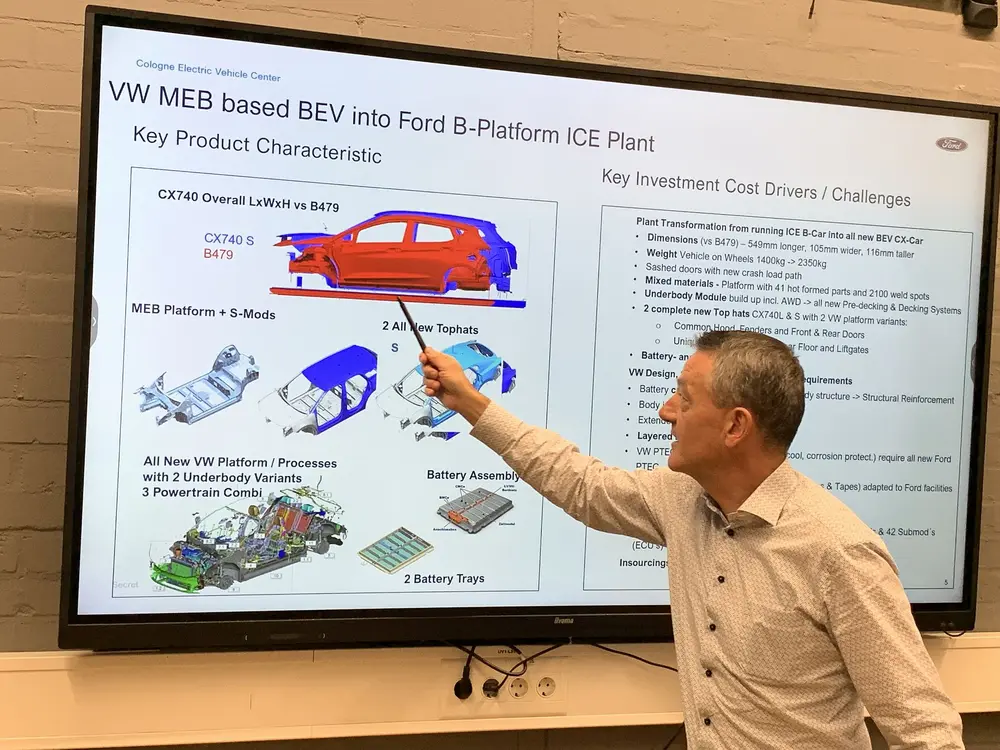
Productie-engineering & digitale mens-machinecommunicatie
De activiteiten van het Ford Cologne Electric Vehicle Center beperken zich echter niet tot de productie van de Explorer en de Capri. In Keulen – waar sinds 1998 trouwens het hoofdkwartier van Ford Europe is gevestigd – bevindt zich immers het Ford-EV-centrum voor digitale ontwikkelingen. Lees: onderzoek en ontwikkeling met het oog op digitale mens-machinecommunicatie. Niet enkel wat de communicatie tussen bestuurder en voertuig betreft. Ook – en belangrijk wat productie-engineering betreft – hoe de mens (werknemer) efficiënt in verbinding kan staan met de (productie) machines.
In Keulen – waar sinds 1998 het hoofdkwartier van Ford Europe is gevestigd – bevindt zich het Ford-EV-centrum voor digitale ontwikkelingen
In het Ford Cologne Electric Vehicle Center is men daarbij getuige van sterke implementatie van zelflerende machines en autonome transportsystemen. Waarbij een omvangrijk realtimegegevensbeheer een integraal ‘werkmiddel’ werd om de verschillende productieprocessen nog efficiënter te laten verlopen. Voor de assemblage van de elektrische Explorer en Capri heeft de productie-engineering bij Ford nieuwe cognitieve en collaboratieve robots geïnstalleerd en nieuwe augmented reality-toepassingen bedacht ter ondersteuning van de werknemers. Anders gezegd: de efficiëntie van data-uitwisseling wordt gestimuleerd door het structureel delen van ervaringen uit de realtimeproductie.
Gigantisch touchscreen
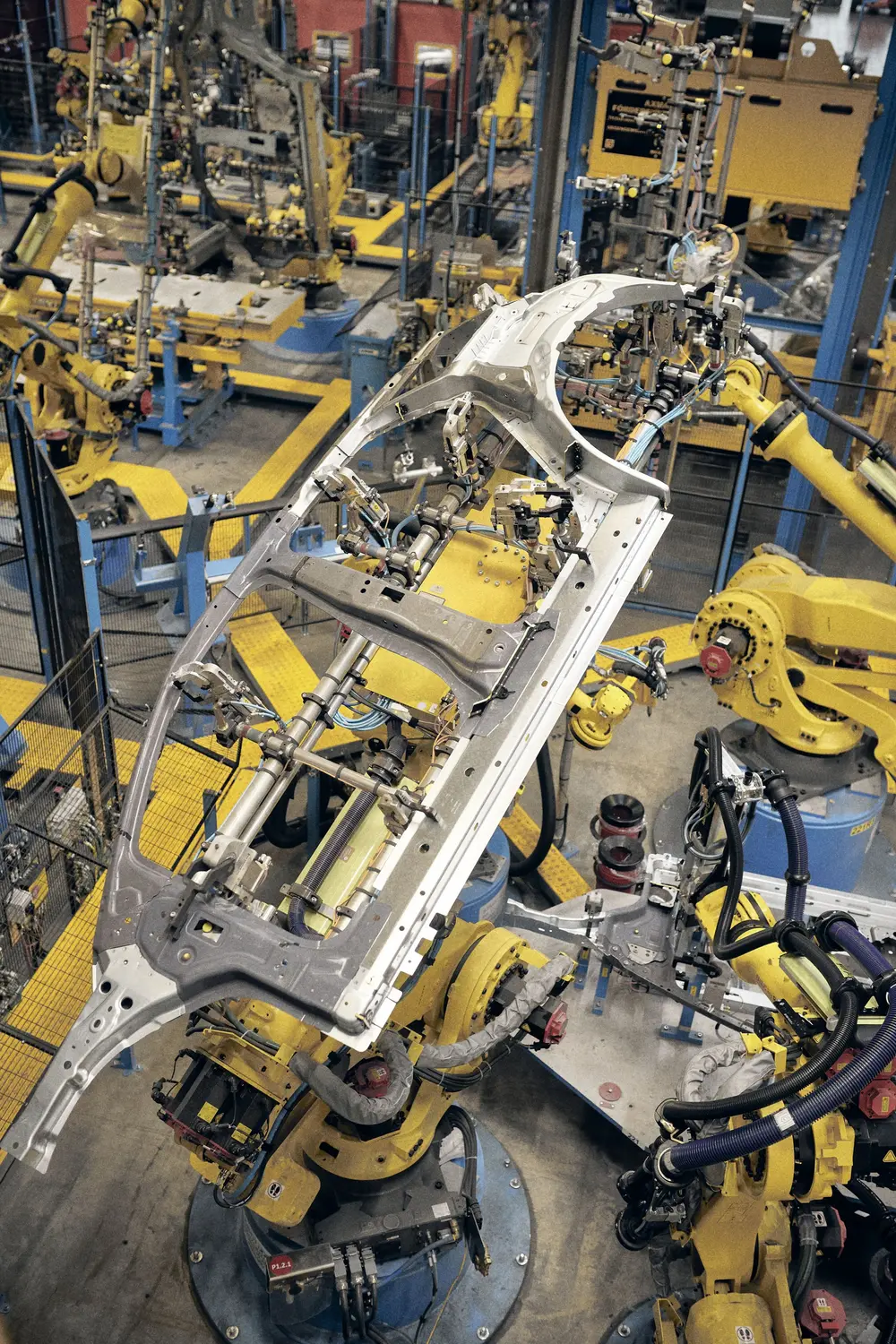
In verband met dit laatste toont Vic Daenen op een gigantisch groot aanraakscherm de striktheid waarmee in het nieuwe controlecentrum het complete productieproces wordt opgevolgd en gecoördineerd. Het hele montageproces wordt trouwens in real time in beeld gebracht. Met een duidelijk zicht op de hoeveelheden van elk onderdeel en elke moer bij elk werkstation. Met voor alle werkstations de informatie over gereedschappen, de toelevering van materialen en onderdelen. Met controle ook op de werkveiligheid. Een deel van de informatie-input komt daarbij van medewerkers die vanop hun werkplek aan de montagelijn de status kunnen doorgeven. Omdat elke stap van het productieproces zo digitaal in beeld wordt gebracht – en ook te controleren is – hebben we het kwaliteitsniveau opgevoerd, verduidelijkt Daenen.
Huidige productiecapaciteit: 630 wagens/dag
Toen in Keulen de Ford Fiesta van de assemblagelijn werd gereden, werkten hier 4.500 mensen. Vandaag zijn er nog 2.600 mensen verantwoordelijk voor de productie. Verdeeld over twee shifts kunnen 250.000 auto’s per jaar worden gebouwd. Of hoe de productiecapaciteit van Ford Keulen is gedaald van 450.000 naar 250.000 auto's per jaar.
In het huidige 2-shiftstelsel kunnen er dagelijks tot 630 auto’s gebouwd worden, waarvan voorlopig 200 Capri ’s. Volgens Daenen bestaat er wel mogelijkheid om in dat 2-shiftstelsel de dagelijkse productiecapaciteit op te trekken tot 700 stuks. En, mochten die 700 stuks niet volstaan om aan de marktvraag te voldoen, kunnen we op de huidige montagelijn – aldus nog Daenen – de productiecapaciteit opvoeren tot 1.250 wagens/dag. Mits extra mankracht en invoering van een 3-shiftstelsel, welteverstaan.
Transformatie van ICE naar BEV in een brownfield plant
In Keulen werd ruim 40 jaar de Fiesta gebouwd op een dubbele assemblagelijn. Als een ICE-gepowerde tot het B-marktsegment te rekenen model. Het betrof een 100% Ford engineered model. Waarbij tijdens de ontwikkeling ook rekening was gehouden met vereenvoudigde montage en verminderde arbeidsintensiviteit. In juli 2023 liep de laatste Fiesta van de montageband. Om de elektrische Explorer en Capri te kunnen bouwen, moest deze brownfield plant in een korte tijd omgevormd worden tot een moderne EV-productie-eenheid.
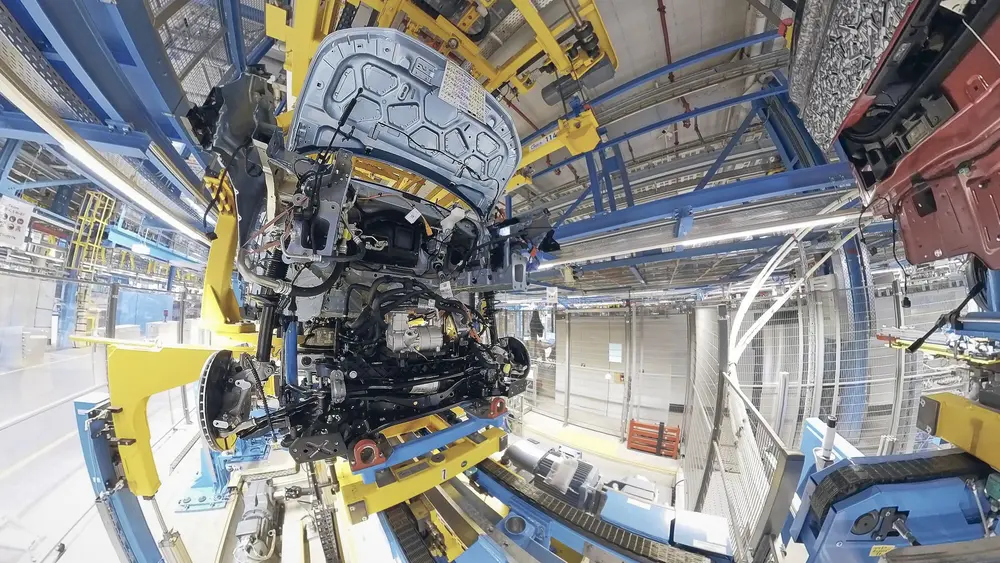
“Normaal gezien hadden we zes maanden eerder al onze eerste Explorers kunnen bouwen”, zegt Daenen. “Echter, pas in juni ll. hebben we officieel de Explorer-productie kunnen aanvatten, enkele weken later gevolgd door de eerste Capri’s.”
Daenen maakt duidelijk hoe complex het is om in een bestaande brownfield plant de transformatie van ICE- naar BEV-productie door te voeren. “Vooreerst was de Fiesta een B-segmentwagen. De BEV Explorer en Capri die we vandaag bouwen, zijn royaler bemeten C-segmentauto’s. Verder gingen we over van een dubbele montagelijn (Fiesta) naar een enkele montagelijn voor de Explorer en Capri vandaag. Ook hadden we niet langer te maken met de door ons zelf ontwikkelde en eenvoudige, minder arbeidsintensieve (Fiesta-)assemblage. De Explorer en Capri worden immers gebouwd op het VW-MEB-platform. Wat ons confronteerde met een moeilijker en arbeidsintensievere assemblage als gevolg van een duidelijk platformgerichte VW-aanpak.”
Complexe software en twee culturen
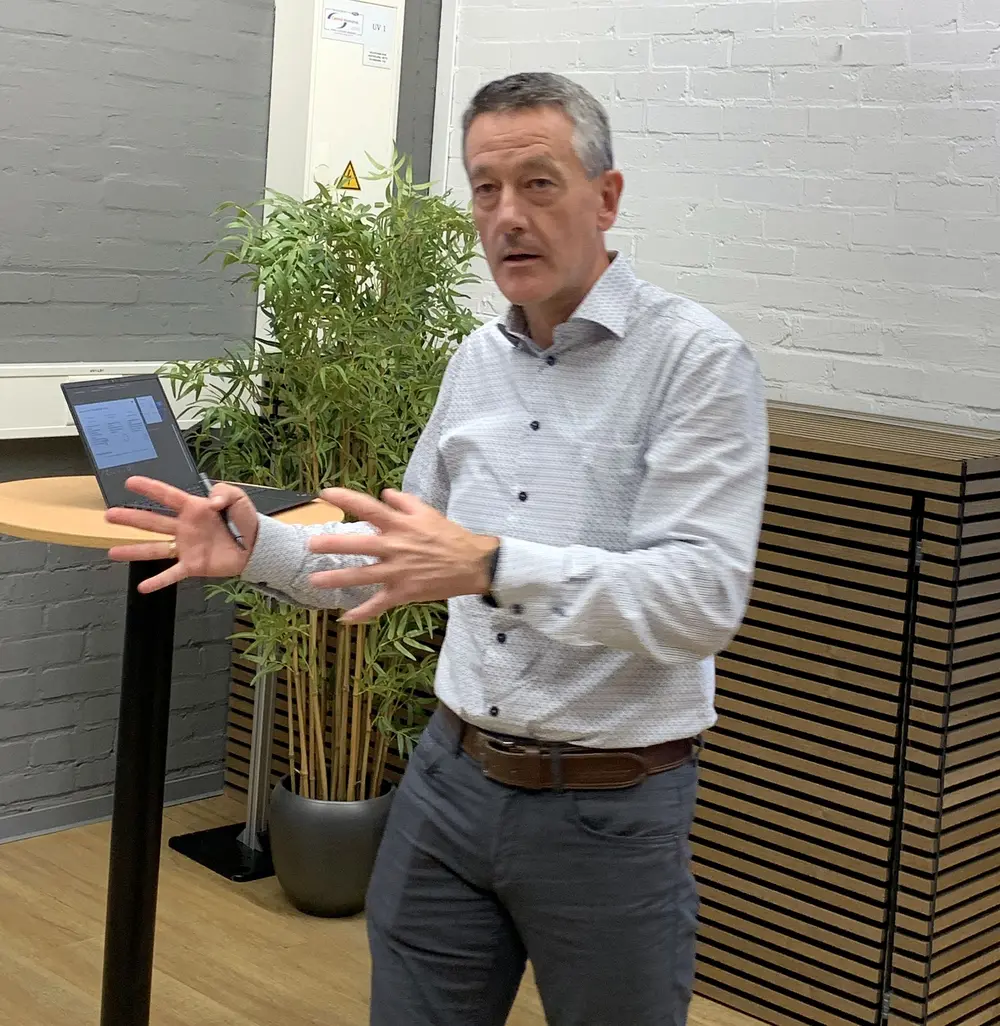
“We kregen dus te maken met twee culturen die hier moesten samenvloeien”, gaat Daenen verder. “Wij bij Ford kennen een productiekostgedreven cultuur. Daartegenover staat de platformgedreven cultuur van VW, die economische schaalbetrachtingen beoogt. Wij hebben hier decennialang de compacte Fiesta geassembleerd. Dit in het Europa waar de hoge loonkost zogezegd het struikelblok vormde om betaalbare compacte auto’s te bouwen. Onze productkostgedreven efficiëntie heeft het tegendeel bewezen.”
“Overigens werden we bij het opstarten van de Explorer- en Capri-productie én bij de implementatie van het VW-MEB-platform – naast ingewikkeldere (dan de Fiesta) en arbeidsintensievere assemblage – ook nog eens geconfronteerd met de veel complexere software die bij Volkswagen gehanteerd wordt”, zo gaat Danen verder. “Bij VW is er binnen dat platformgegeven trouwens sprake van 54 processoren. Wij bij Ford kozen voor een vereenvoudigde benadering, met twee hoofd-CPU’s en 42 subgroepen. De voor deze aanpassingen noodzakelijke softwareaanpassingen verliepen gecompliceerd, maar waren uiteindelijk toch succesvol.”
Artificiële intelligentie & nieuwe robots
Om de productiekwaliteit van de Explorer en Capri in het Electric Vehicle Center te garanderen, wordt een beroep gedaan op geavanceerde artificiële intelligentie en zijn honderden gechoreografeerde (zelflerende) robots geïnstalleerd. De productie wordt dus uiteindelijk geschraagd met zelflerende machines en een totaal van meer dan 600 nieuwe robots die las-, snij-, stofvrijmakende, verf- en smelttaken uitvoeren.
Voor de samenstelling van de onderbouwstructuur (85 onderdelen per structuur) wordt in Keulen een beroep gedaan op 126 lasrobots, 143 handlingrobots, 10 lijm- of adhesierobots, 13 puntlasrobots en 4 meetrobots. Samenstelling van die onderbouwstructuur vraagt 1.938 puntlassen, 127 bouten, 35 meter lijm- of adhesiematerialen en 24 lasmoeren. In de bodyshop lassen 112 robots, werken 62 handlingrobots, 20 lijm- of adhesierobots, 2 puntlasrobots, 8 meetrobots, 8 lasersoldeerrobots en 10 schoonmaakrobots…
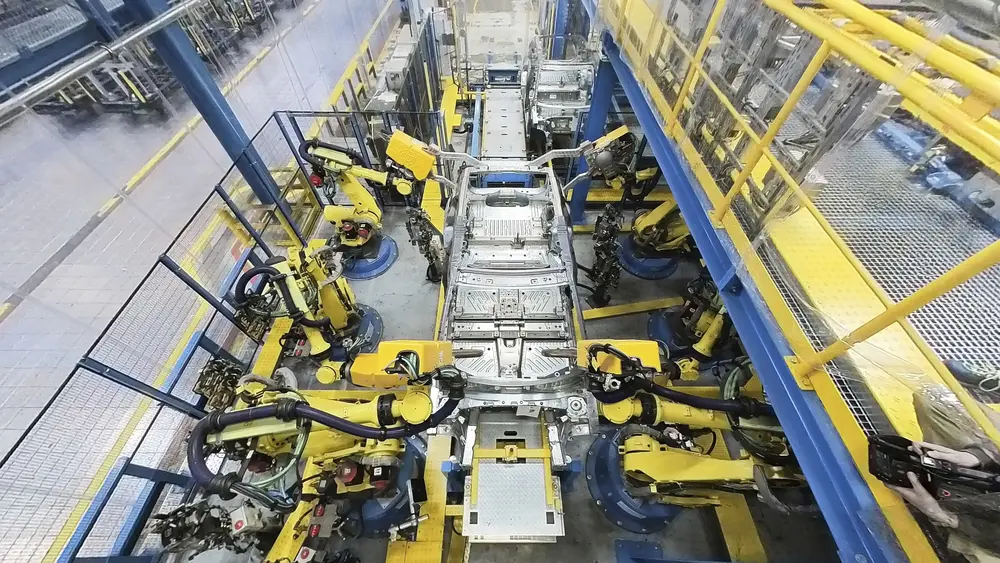
China is de EV-benchmark
Terwijl Vic Daenen ons deskundig uitleg verschaft over het reilen en zeilen van de productiesite waar hij al tien jaar het commando voert, blijft de vraag ons onophoudelijk door het hoofd spelen: de Europese auto-industrie kreunt dezer dagen onder de slabakkende EV-verkoop, fabrieken dreigen te sluiten … In dat economisch klimaat investeert Ford buitengewoon zwaar in een nieuwe productielijn om twee nieuwe EV’s op een moeilijke markt te lanceren. Twee middelgrote SUV’s die bovendien thuishoren in een marktsegment waarin – ook in het BEV-deel – het aanbod al overweldigend is. Waarom heeft men bij Ford niet geopteerd om hier in Keulen compactere (naar Fiesta-maatstaven) en minder dure (dan Explorer en Capri) modellen te bouwen?
Daenen: “Met in Europa gebouwde, elektrische wagens die minder dan € 35.000 kosten, valt niet te concurreren met Chinese autobouwers"
Daenen: “Omdat er met in Europa gebouwde, elektrische wagens die minder dan € 35.000 kosten, niet te concurreren valt met Chinese autobouwers. Voor iets duurdere en ruimere auto’s als de Explorer en de Capri ligt dat iets eenvoudiger... (stilte) … al zeggen we beter: minder moeilijk. Met in Europa beter in de markt liggende modellen als de Explorer en de Capri en ‘bijgestaan’ door onze ‘productiekostgedreven’ assemblage denk ik dat we in het Explorer/Capri-marktdeel een beetje van onze achterstand op de Chinese constructeurs kunnen goedmaken. Want, laat er ons niet moeilijk over doen, China is de EV-benchmark."
"Ze hebben de grondstoffen, beheersen zowat de complete EV-toeleveringsketen, genieten overheidssteun en worden niet (of veel minder streng dan in Europa) gehinderd door CO2-normgeving. Bovendien zijn ze al langer dan wij drukdoende in de auto-elektrificatie. Dat heeft hun een aanzienlijke elektrotechnische voorsprong opgeleverd. Kijk maar naar hun batterijtechnologie waarmee ze zich ten opzichte van Europese constructeurs een gevoelige voorsprong hebben opgebouwd. En dan wil ik het – wat die Chinese voorsprong betreft – nog niet hebben over het veel hoger uitvallend gemiddeld aantal werkuren en de lagere loonkosten van en voor Chinese werknemers. Of de energiekosten in China die – in vergelijking met Europa – veel lager uitvallen”", besluit Daenen.