Lagers sleutels tot succes elektrische voertuigen
De auto-industrie staat voor haar grootste omwenteling in meer dan honderd jaar. De elektrificatie noopt constructeurs om terug naar de tekentafel te gaan en tabula rasa te maken van de wagen die ze kenden. Dat geldt in feite ook voor heel wat componenten. Hoewel elektrische voertuigen (EV's) nog altijd lagers nodig hebben, zijn het er minder en vooral andere. Door te spelen met nieuwe materialen en nieuwe afdichtingsontwerpen moet men gehoor geven aan twee uitdagingen waarmee lagers geconfronteerd worden: de reductie van wrijving en de bescherming tegen zwerfstromen.
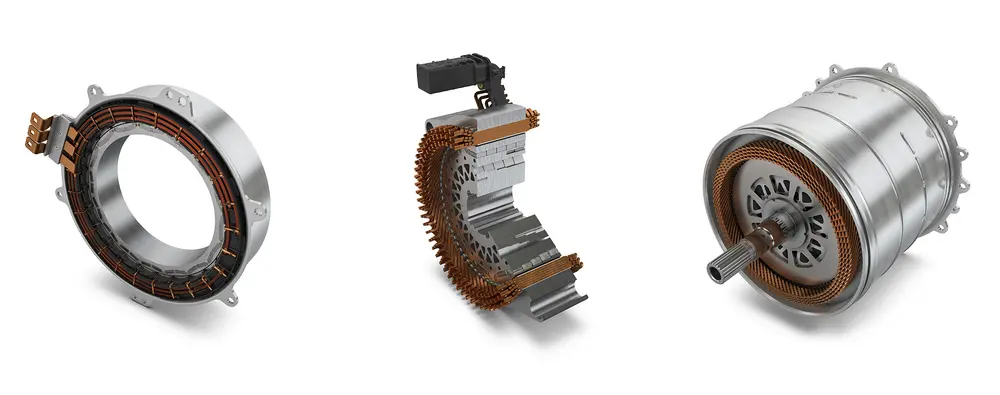
Lagertechniek bij verbrandingsmotoren
Lagers vind je normaal overal in de wagen terug: aan de wielassen, in de versnellingsbak, aan de distributieriem … In functie van hun taak en plaats, varieert het type lager dat gebruikt wordt. De meest voorkomende zijn kogellagers. Zij zorgen voor de hoogst mogelijke efficiëntie bij de wiellagering en als druklager in de koppeling. Wanneer er minder plaats ter beschikking is en het lager toch hoge belastingen moet torsen, zijn rollagers zoals kegelrollagers of cilinderlagers dan weer de betere keuze. Dit geldt vooral in de versnellingsbak, waar op bepaalde plaatsen ook naaldlagers een optie zijn als er maar een heel beperkte ruimte beschikbaar is.

Lagertechniek bij elektrische voertuigen
Waarin verschilt de aandrijflijn van EV's nu wanneer we inzoomen op lagers? Allereerst zijn er een aantal lagers minder nodig in een EV, gemiddeld 5 à 10. De aandrijflijnen mogen dan mechanisch eenvoudiger zijn, toch brengt het ook een aantal uitdagingen met zich mee. De elektromotoren zijn immers ontworpen om aan zeer hoge toerentallen te werken. Vandaag gaat het al om 20.000 omwentelingen per minuut, bij toekomstige ontwerpen zou dit verder oplopen tot 25.000 à 30.000. Daarnaast doet men er alles aan om de grootte en het gewicht van de aandrijflijncomponenten te beperken.
De hogere belastingen en rotatiesnelheden vragen om grote lagers die snel kunnen roteren. Dat stelt hogere eisen aan de betrouwbaarheid en robuustheid van lagers. Een tweede element om rekening mee te houden is de wrijving. Hoe meer wrijving, hoe hoger het verbruik zal liggen en de actieradius van EV's dus zal slinken. Lagers in EV's zullen vanwege de beperkte actieradius dus nog meer wrijving moeten wegnemen dan in voertuigen met verbrandingsmotoren. Wrijving is ook rechtstreeks gelinkt aan het gewicht. Hoe meer de componenten van de aandrijflijn wegen, hoe hoger de nood aan wrijvingsreductie zal zijn. Dit zal het hardst spelen bij wiellagers, waar de belastingen het grootst zijn.
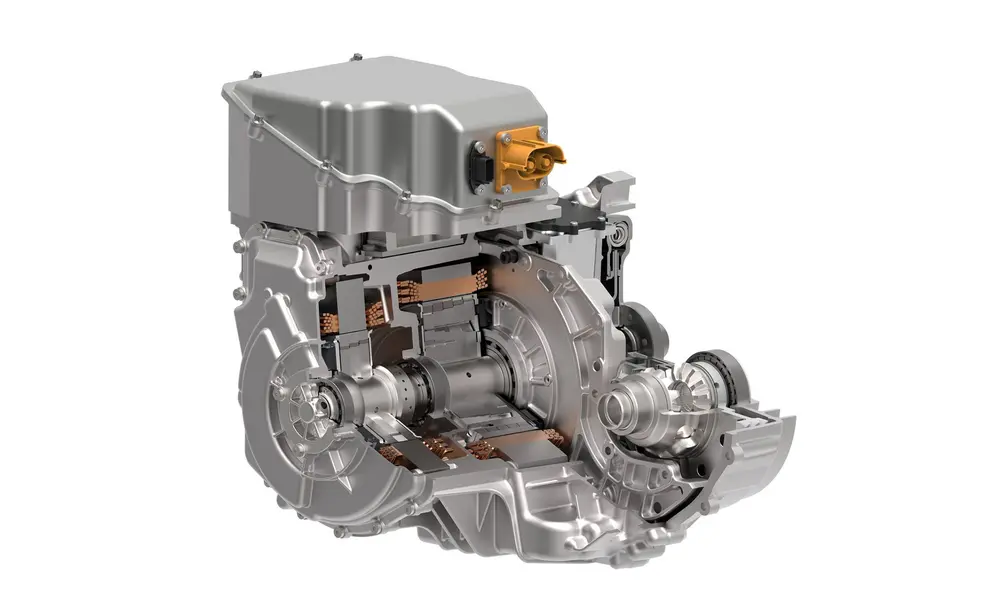
oplossingen
Gebruik van keramiek
Vooral voor de lagers in en rond de elektrische motor zelf wordt gekeken naar een ander materiaal. In plaats van het klassieke metaal is keramiek immers een beter alternatief om tegelijk aan hogere snelheid te roteren en de frictie die daarbij vrijkomt te verlagen. Zelfs wanneer de smering perfect gebeurt, zal er onder hoge temperaturen en hoge belasting altijd wel staal-op-staalcontact ontstaan. In vergelijking met staal zal er bij keramiek een frictiereductie optreden van gemiddeld 5 à 10%.
Ten tweede is keramiek geen geleidend materiaal. Belangrijk, want zwerfstromen zijn voor lagers de belangrijkste oorzaak van faling in EV's. Die zwerfstromen worden veroorzaakt door de hoge en snelle schakelspanningen van de omvormer van de elektromotor, voornamelijk wanneer er sprake is van een klein volume en een groot vermogen. Dit zal geen issue zijn wanneer het vermogen laag is, maar wel als er 100 kW gevraagd wordt. Wanneer een zwerfstroom door een stalen lager gaat, ontstaat er schade aan het oppervlak (stroomdoorslag) met meer wrijving en trillingen en een vroegtijdige uitval tot gevolg. Keramiek is hier beter tegen gewapend.
Het nadeel van keramiek is echter de kostprijs van het materiaal. Er hangt een hoger prijskaartje aan. Verwacht wordt wel dat door een toename in volume van keramische lagers door de opkomst van elektrische wagens, de prijzen zullen dalen. Vandaag vinden ze vooralsnog toepassing in lucht- en ruimtevaart. Wat wel al veelvuldig toegepast wordt en gunstiger geprijsd is, zijn hybridelagers met stalen ringen en keramische kogels. Ook daarbij worden voordelen behaald op het gebied van lagere wrijving en lagere temperatuur bij hoge toerentallen en minder risico op lekstromen.
In vergelijking met staal zal er bij keramiek een frictiereductie optreden van gemiddeld 5 à 10%
Aanpassing interne geometrie en afdichtingen
Om onder alle omstandigheden goed te presteren in EV's zullen lagers vooral ook robuust moeten zijn. Om die betere prestaties te halen werken lagerfabrikanten aan verbeteringen van de interne geometrie en afdichtingen. Zo wordt er bv. gewerkt aan een nieuwe architectuur voor de wiellagers om te compenseren voor de kortere transmissie in een elektrische aandrijflijn. Daarnaast wordt ook vaker gebruik gemaakt van de vierde generatie lagers, waarbij de lagering is geïntegreerd in de aansluitconstructie. Dit levert een gewichtsbesparing op, een betere geometrie en dus ook minder frictie.
Coatings voor lagers
Vandaag worden in beperkte mate coatings toegepast op lagers in voertuigen. In EV's zullen lagers wel zwaarder op de proef gesteld worden dan in voertuigen met een klassieke verbrandingsmotor. Een coating kan dan dienen als corrosiebescherming, om ‘creep’ te verhinderen, de dunne oliefilm vast te houden, geluid te beperken en adhesie aan het oppervlak van lagers te voorkomen. Keramische coatings kunnen een antwoord bieden op zwerfstromen. Op korte termijn kan een coating dus zeker bijdragen tot beter presterende lagers. Op lange termijn moet er dan wel een manier gevonden worden om te evolueren van een batch naar een continu proces om coatings op een kostenefficiënte manier aan te brengen.
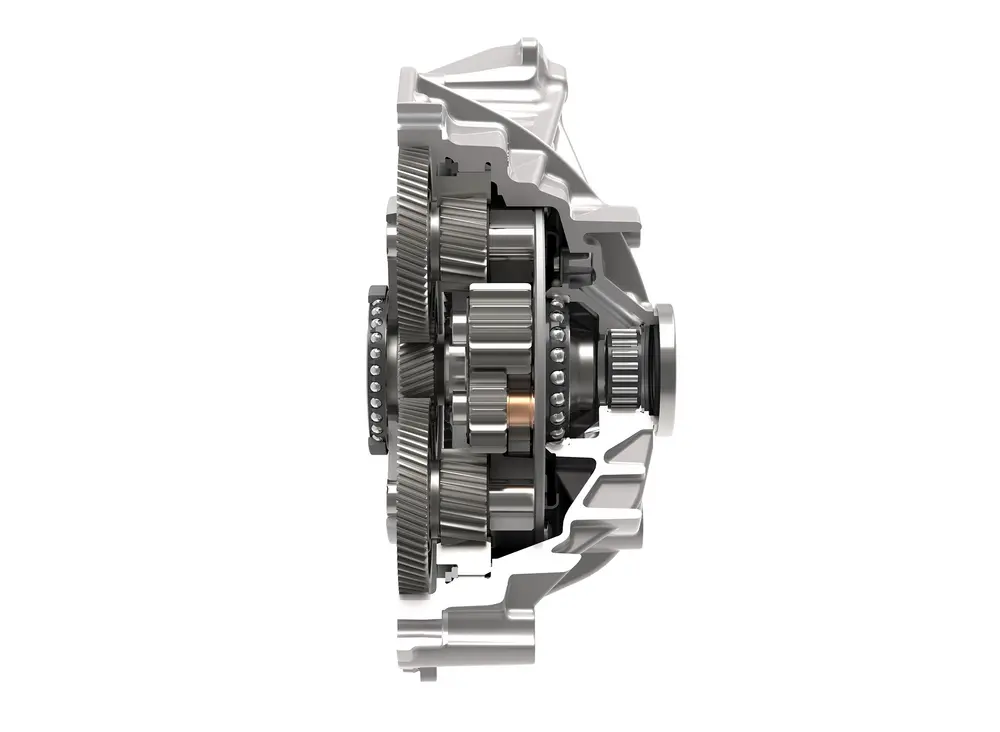
Conclusie
Het belang van lagers in EV's kan niet overschat worden. De reductie van wrijving is een van de belangrijkste manieren om sprongen voorwaarts te zetten in de actieradius van EV's. Uiteraard wordt er ook gekeken naar compactere en betere batterijen, maar verbeteringen in de energiedichtheid van batterijen zullen nog onderzoek vragen. Lagers die bestand zijn tegen hoge snelheden en die ultralage wrijving hebben, kunnen vandaag al helpen om meer kilometers uit dezelfde batterij te halen.
Keramiek lijkt wat dat betreft de beste keuze. Maar fabrikanten werken ook aan de ontwikkeling van verbeterde interne geometrieën en afdichtingen om wrijving te reduceren. Verder kunnen coatings interessant zijn om de belasting bij hoge snelheden terug te brengen. Daarnaast moet uiteraard gekeken worden naar compatibele en hoogperformante smeermiddelen.
Wat verandert er in de werkplaats?
Wat lagertechniek betreft eigenlijk weinig. Uit welk materiaal het lager ook bestaat, staal of keramiek, de demontage en montage kan eigenlijk op dezelfde manier verlopen. Lagerfabrikanten hebben er van bij het ontwerp rekening mee gehouden dat deze componenten makkelijk te vervangen moeten zijn.
Met medewerking van NTN-SNR Roulements, Schaeffler en SKF