Moins de soudage, plus de collage
Techniques d'assemblage innovantes SUR le marché de la réparation automobile

L'apogée du soudage dans le secteur automobile s'éloigne peu à peu des actuels techniques de réparation. Pour l'aluminium, à l'instar de l'aviation, cette technique d'assemblage a déjà été définitivement écartée, concernant l'acier, on se dirige lentement dans cette direction également. Il est important de remarquer que tout apport de chaleur génère des points de faiblesse dans l'assemblage. La colle 2 composant a pris la place vacante, il est vrai en combinaison avec d'autres alternatives, comme les rivetages SPR (rivet auto-perceur) et BSF (rivet à rupture de tige). Parce que se fier à la seule force d’adhérence de la colle n'est jamais une bonne idée.
quelques explications concernant Le succès des colles

Dans les structures de carrosserie actuels, les adhésifs font de plus en plus partie de la technique d'assemblage utilisée par les constructeurs pour fixer les tôles et les pièces entre elles. Deux raisons expliquent ce phénomène.
Matériaux hybrides
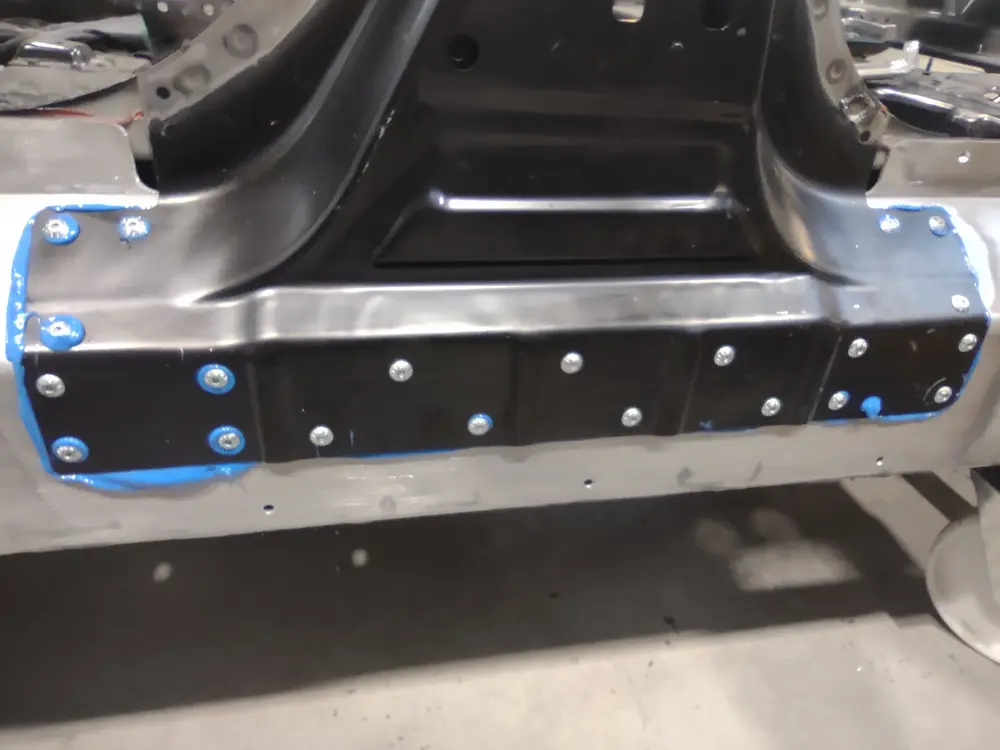
Aujourd'hui, les ingénieurs en structure travaillent avec des matériaux différents. Ceci est particulièrement fréquent dans les renforts: une combinaison de différents types d'acier, d'aluminium et même de carbone dans la composition d'une pièce n'est plus une exception. Toutefois, ce mélange de matériaux entraîne des zones de tension différentes.
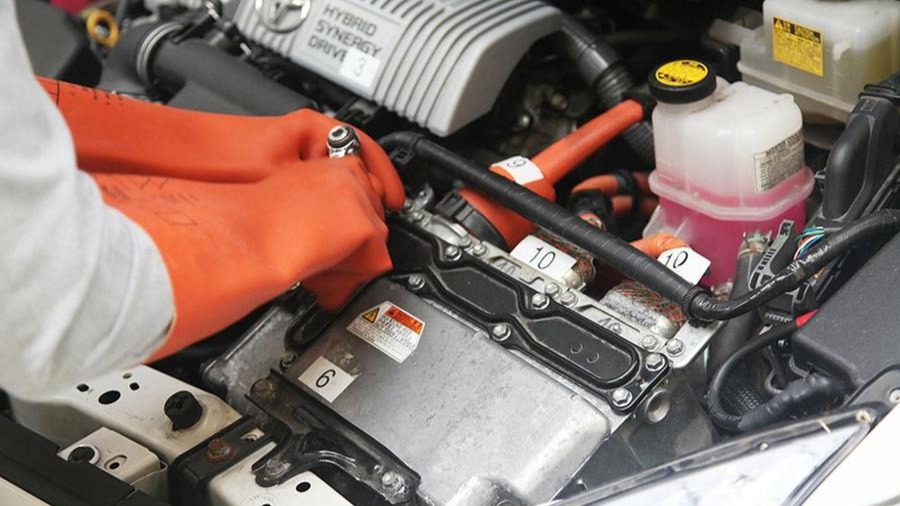
C'est pourquoi il est devenu essentiel d'éviter entre autres la corrosion de contact lors de l'assemblage de deux ou plusieurs pièces de ce type. Dans cette histoire, un adhésif 2 composants joue le rôle de tampon. En utilisant l'adhésif comme une sorte de couche isolante, vous évitez que deux – ou même trois – matériaux différents n'entrent en contact direct l'un avec l'autre. La corrosion de contact ne peut donc plus se produire.
Intégrer plus de rigidité
La carrosserie d'une voiture est constamment soumise à des forces, qui vont dans toutes les directions. L'assemblage ne doit donc pas être trop fragile, sinon il se brisera simplement sous l'effet de la torsion et de la flexion créée. La colle ajoute de la rigidité à un assemblage. Supposons un assemblage par rivetage qui maintient deux tôles ensemble. Sans colle, cet assemblage n'a pas la rigidité nécessaire pour absorber les chocs, par exemple. L'orifice (perçage) dans lequel se trouve le rivet s'arracherait. Et vous ne voulez pas ça, bien sûr.
La colle et les rivets forment un duo idéal: les rivets maintiennent les pièces en place et la colle absorbe les vibrations
La colle seul ne peut satisfaire à tous les efforts mécaniques
L'encollage peut présenter des avantages très intéressants, mais il faut absolument le combiner avec d'autres techniques d'assemblage. Sinon, vous risquez d'avoir de très mauvaises surprises. Différentes contraintes agissent sur un assemblage (voir encadré) et la colle ne réagit pas de la même manière à toutes les contraintes. Au contraire. Les meilleures performances sont obtenues lorsque la charge est répartie sur toute la surface de la ligne d'adhésion. Ceci est vrai pour les contraintes de traction, de compression et de cisaillement. À l'inverse, la rupture et les contraintes de cisaillement peuvent entraîner une défaillance prématurée de l'assemblage. En effet, dans ces cas, la contrainte se concentre généralement de manière unilatérale sur la face extérieure. La colle ne réagit pas aussi bien. Cela explique immédiatement pourquoi la colle et les rivets (nous y reviendrons plus tard) forment le duo idéal: tandis que les rivets maintiennent les pièces en place, la colle apporte la résistance supplémentaire nécessaire pour absorber les vibrations et les chocs.
CONTRAINTES POSSIBLES QUI SE PRODUISENT DANS LES JOINTS DE COLLE
• Résistance à la traction. Celle-ci s'étend uniformément sur la surface et suit une direction droite qui s'éloigne de l'assemblage.
• Résistance au glissement. Celle-ci se produit lorsque deux feuilles glissent l'une sur l'autre dans une direction horizontale.
• Résistance au pelage. L’assemblage est soumis à une charge inégale sur la ligne d'adhésion. Mais comme l'un des deux substrats est flexible, la contrainte est concentrée sur le bord de l'assemblage, encore plus que dans le cas d'une fission.
• Résistance à la fission. Similaire au pelage. Là encore, Il s'agit d'une forme de contrainte moins favorable aux adhésifs car la force de traction s'exerce sur les deux bords de l'assemblage. Se produit avec deux substrats rigides.
types de colle 2 COMPOSANTS
Les colles sont des produits chimiques dont la composition varie d'un fabricant à l'autre. La plupart des colles 2 composants utilisées dans l'industrie automobile sont fabriquées à base d'époxy et d'un catalyseur. L'offre est large et on modifie constamment la composition pour améliorer les performances.
L'ajout de microbilles de verre constitue par exemple une évolution dans ce contexte. Celles-ci doivent garantir qu'il y a une épaisseur minimum entre les deux tôles à coller et que l'adhésif ne peut pas être écrasé complètement. De cette façon, ils assurent une adhésion optimum.
Quelle colle choisir?
Compte tenu de l'abondance de l'offre et des conséquences négatives possibles d'un mauvais choix, nous vous recommandons vivement de ne pas faire d'expérience vous-même: c'est le fabricant qui indique dans les infos techniques quelle colle doit être utilisée. Suivez-le dans cette démarche, car en dehors des différences propres à chaque marque, il existe une distinction générale entre une colle 2 composants structurelle et une autre non structurelle.
La force d'adhérence du premier type de colle, plus coûteux, est supérieure à celle du second. Pour cette raison, la colle 2 composants non structurelle ne doit être utilisée que pour coller des panneaux ne subissant que peu de contraintes, comme par exemple, certains endroits d'un panneau d'aile arrière, mais certainement pas pour des pièces portantes. Vous devriez laisser au fabricant le soin de prendre ce genre de décision, qui nécessite des connaissances spécialisées.
La colle 2 comosants non structurelle ne doit absolument pas être utilisée pour les pièces portantes
Combinaison avec SPR et BSF
Comme expliqué précédemment, vous devez toujours combiner le collage avec une deuxième technique d'assemblage. Étant donné que les équipementiers les appliquent souvent dans leurs assemblages d'origine, il s'agit généralement, dans la pratique, de rivets SPR auto-perceurs et BSF rivets à rupture de tiges (break stream fasteners).
rivets SPR
Un SPR est un rivet avec un revêtement spécial qui est pressé au travers les tôles. Il n'y a donc pas de pré-perçage. À l'arrière, le rivet est serré en place à l'aide d'un outil à presset et d'une matrice personnalisée. En d'autres termes, si vous voulez utiliser un SPR, vous devez avoir accès aux deux côtés du panneau.

Pour remplacer un SPR, aujourd'hui deux choix sont possibles: soit un autre SPR, soit un FFR (flow form rivet rivet dont la malléabilité est supérieure). Cette deuxième option est relativement récente. Il s'agit d'utiliser un dispositif spécial doté d’un poinçon calibré en acier de très haute résistance et d’une matrice afin de réaliser l’ajustage précis du perçage déjà existant et dans la nouvelle pièce. L'avantage de cette méthode est que vous pouvez utiliser le perçage existant pour riveter à nouveau les panneaux avec le FFR. Dans le cas d'un nouveau SPR, e placement de celui-ci s’effectue à une distance suffisante du trou laissé par l’extraction du rivet d’origine.
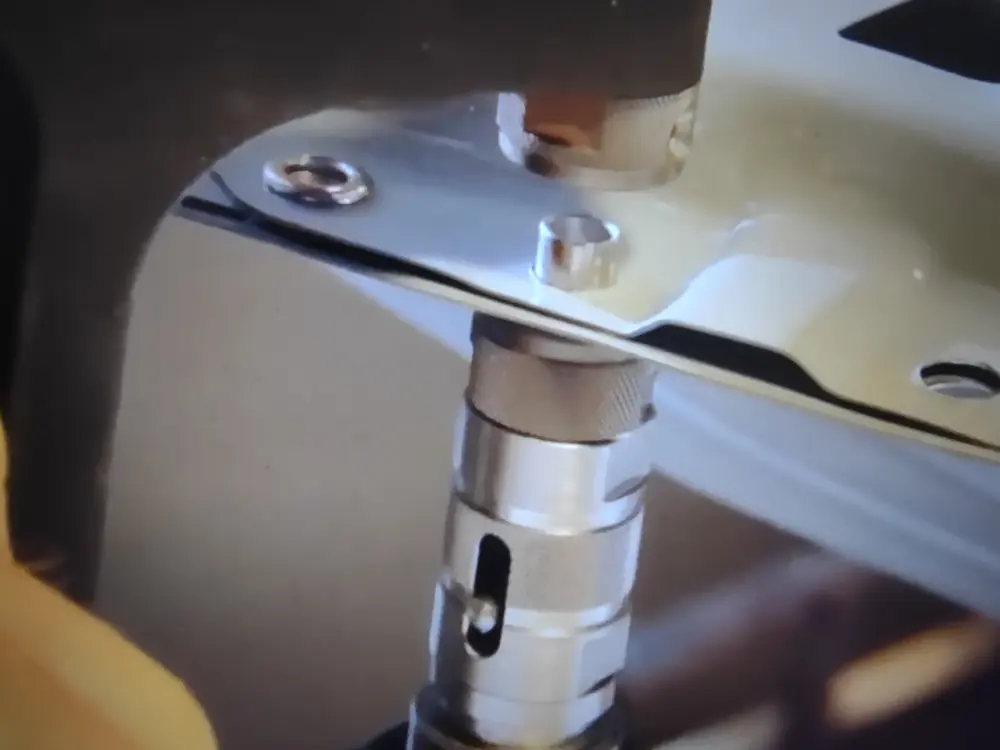
BSF
BSF est un nom collectif pour un autre type de rivets. Les hemlocks et les monobolts, entre autres, appartiennent à cette catégorie. Contrairement aux SPR, ce type d'appareil nécessite de percer un trou au préalable. Une autre différence est que vous n'avez pas besoin de pouvoir accéder à l'arrière. C'était le cas pour les SPR mais aussi pour les FR. Cela signifie donc aussi que vous ne pouvez pas remplacer un BSF par un FFR ou un SPR. Le vissage des BSF se fait avec une pince à tirage.
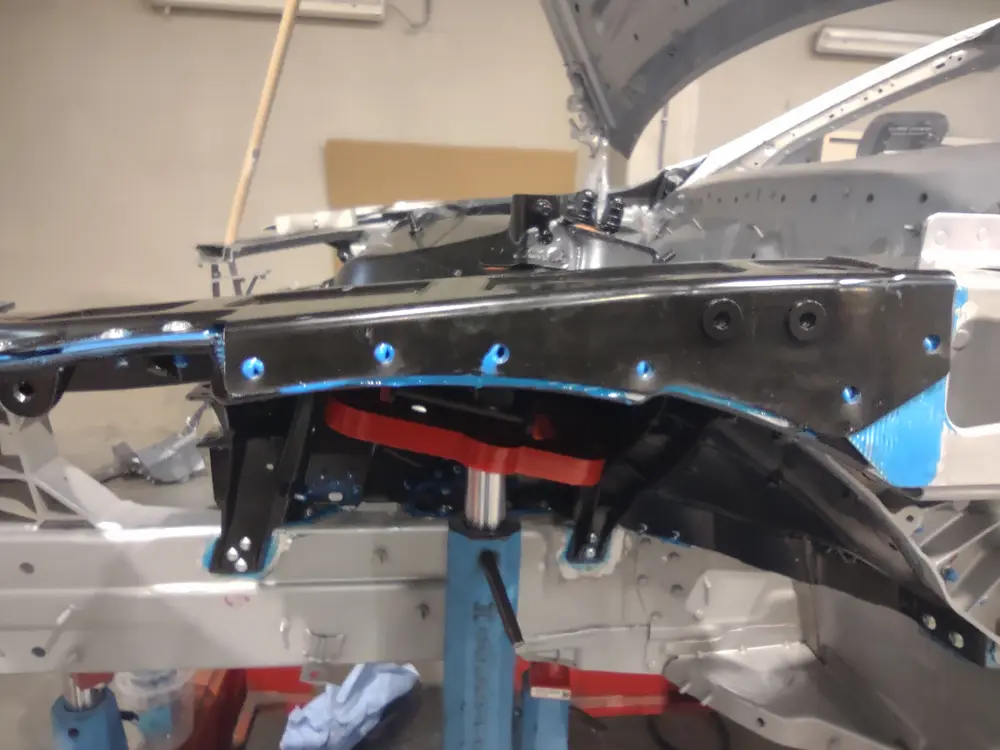
Une bonne préparation est essentielle
En quelques années, la gamme de rivets – surtout avec l'avènement des FFR – a énormément augmenté. Parmi les SPR, vous avez certainement déjà une quinzaine de types. Dans certaines ailes arrière, vous rencontrez jusqu'à sept types. Dans certains assemblages d’ailes arrière, vous rencontrez jusqu'à sept types différents. Le nombre de BSF, d'ailleurs, n'est pas beaucoup plus bas. La différence ne réside pas seulement dans la longueur ou la force de compression, mais aussi dans l'aspect esthétique. En fonction de l'emplacement du panneau et de sa visibilité, on peut choisir, par exemple, un rivet à tête zinguée et à bords fraisés.
Comme pour le choix de la colle, c'est au constructeur d'indiquer quel rivet doit être choisi pour remplacer l'ancien assemblage. Étant donné la grande variété, cela implique une certaine préparation. Sachez qu'après avoir appliqué la colle – les infos techniques indiquent si elle doit être appliquée sur le métal nu ou si un apprêt doit être appliqué au préalable – à une température comprise entre 20 et 23 °C, vous avez environ une heure avant que la colle ne commence à durcir. Par conséquent, disposez tous les rivets à l'avance et mémorisez bien à l'avance l'emplacement de chaque rivet. Sinon, ce sera une course désespérée contre le temps.
En collaboration avec Educam, le centre de connaissance et de formation pour l'automobile et les secteurs connexes (www.educam.be)