La lubrification par ultrasons
Une manière pragmatique de déterminer la bonne quantité de graisse lubrifiante
La lubrification des machines et des installations se fait souvent sur base des heures de fonctionnement. Une approche logique, qui ne tient toutefois pas compte des facteurs dynamiques tels que la (sur)charge, les facteurs environnementaux et la température. Pour éviter une lubrification excessive ou insuffisante, on peut utiliser un équipement à ultrasons. Ces instruments peuvent facilement identifier un niveau de frottement accru dû à une insuffisance ou, au contraire, à un excès de graisse dans un roulement, par exemple. Sur la base des résultats de mesure, le service technique peut alors décider de prendre les dispositions qui s'imposent ou d'ajouter exactement la bonne quantité de graisse.
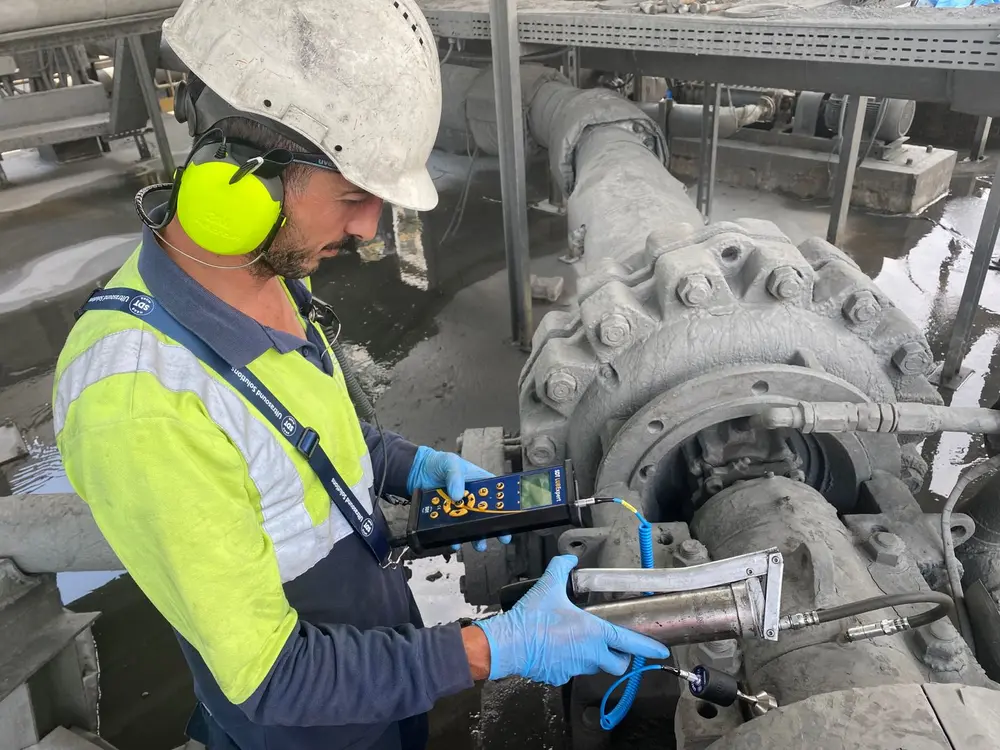
La maintenance de la lubrification est un facteur important dans les applications industrielles pour minimiser les frottements et dissiper de manière optimale la chaleur et la saleté. Dans ce contexte, une bonne lubrification contribue donc à un fonctionnement efficace mais surtout fiable des machines. Les entreprises qui accordent suffisamment d'attention à cet aspect de la maintenance utilisent souvent un calendrier qui précise quel composant de la machine doit être lubrifié et à quel moment. Dans le cas le plus simple, ces intervalles de lubrification sont déterminés par le temps. Par exemple, toutes les semaines, tous les mois ou tous les six mois.
Une approche un peu plus dynamique est la lubrification basée sur le nombre d'heures de fonctionnement; le service technique doit alors garder une trace de ce nombre quelque part. Cette approche permet d'éviter que les machines utilisées de manière irrégulière ne soient lubrifiées trop tôt. Bien entendu, les inspections visuelles et auditives sont également fréquemment utilisées pour vérifier l'état de la lubrification.
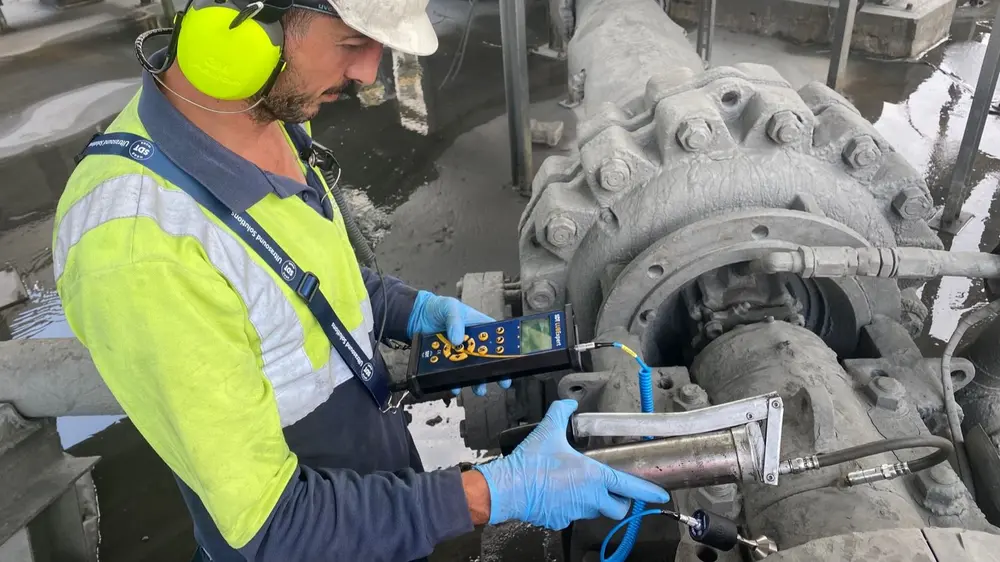
Les différentes méthodes d'inspection ne sont pas nécessairement mauvaises, mais elles ne tiennent pas compte des facteurs qui peuvent modifier le besoin de lubrification. Par exemple, la surcharge de la machine, mais aussi les différences de température ou d'autres facteurs environnementaux. Dans de tels cas, une sous-lubrification peut se produire et la lubrification régulière risque d'être effectuée trop tard. Cela peut entraîner une augmentation des frottements - et donc de la consommation d'énergie -, des niveaux de bruit plus élevés et, en fin de compte, une réduction de la durée de vie des composants.
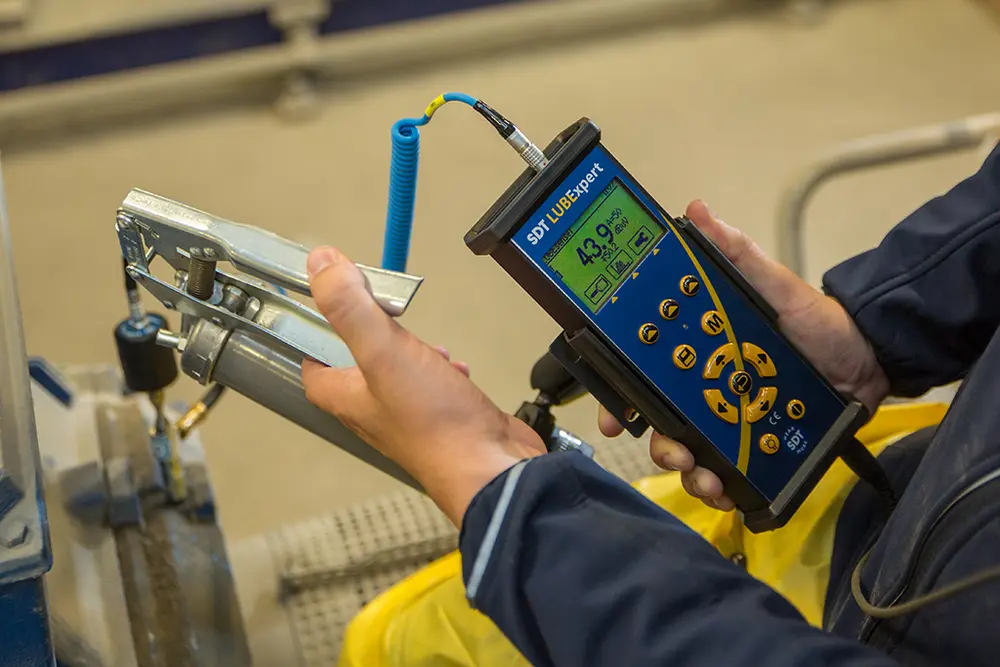
Inspection avec un équipement à ultrasons
Un appareil à ultrasons est un outil typique pour vérifier la quantité de lubrifiant. Dans cet article, nous nous penchons sur des éléments rotatifs où un manque de lubrification entraîne un contact métal-métal, comme c'est le cas pour les roulements. Cette situation provoque des vibrations à une fréquence très élevée, supérieure à 20.000 Hz. Ces vibrations se situent dans le domaine des ultrasons (voir l'encadré) et ne peuvent pas être entendues par l'oreille humaine. En revanche, des appareils à ultrasons spéciaux peuvent détecter cette fréquence. La technologie des ultrasons appartient donc au domaine de la mesure et de l'analyse des vibrations, mais elle est limitée à une gamme de fréquences spécifique: les ultrasons.
Comme pour l'analyse des vibrations, il est possible de visualiser les mesures des appareils à ultrasons sous forme de graphiques. Ceux-ci peuvent être analysés par des spécialistes qui en tirent des conclusions. Si cette méthode est très précise pour identifier toutes sortes de problèmes, elle présente l'inconvénient de nécessiter une analyse préalable par des spécialistes.
La mesure par ultrasons est une forme d'analyse des vibrations, mais dans le spectre des ultrasons
Pour une utilisation pratique immédiate de la technologie, les appareils à ultrasons sont capables de convertir les ondes ultrasonores en signaux audibles grâce à un logiciel d'analyse de spectre. La mesure est effectuée en appliquant une sonde de capteur sur le roulement. Les signaux sonores - reçus par l'utilisateur au moyen d'un casque - sont souvent associés à des informations visuelles sous la forme d'un graphique ou d'un spectre sur un écran. Cette combinaison favorise une perception objective, car l'utilisateur n'a pas à entendre seul - ce qui est souvent plus subjectif - mais peut également vérifier ses observations à l'aide de l'écran.
Par conséquent, presque tout le monde peut utiliser cet équipement pour entendre à l'endroit où le niveau de bruit s'écarte de la norme. Si un écart est détecté, des techniciens formés peuvent encore interpréter l'état du composant concerné à l'aide du graphique et déterminer ensuite les éventuelles mesures de suivi à prévoir.
Qu'est-ce qu'un ultrason?
Les ultrasons font partie du spectre sonore total exprimé en Hz (nombre de vibrations par seconde). L'oreille humaine est capable de capter une partie de ce spectre sonore: typiquement entre 20 Hz et 20.000 Hz. Nous entendons mieux entre 100 et 5.000 Hz. Les sons très graves, c'est-à-dire inférieurs à 20 Hz, ne sont plus audibles mais peuvent souvent encore être ressentis. Les sons dont la fréquence est supérieure à 20.000 Hz sont appelés ultrasons. Ce son est notamment utilisé par certaines espèces animales pour s'orienter, communiquer et naviguer. Dans le secteur médical, il est utilisé dans l'échographie, tandis que l'industrie mécanique utilise les ultrasons à des fins de nettoyage, pour détecter les fuites d'air et déterminer la sur- ou sous-lubrification, entre autres.
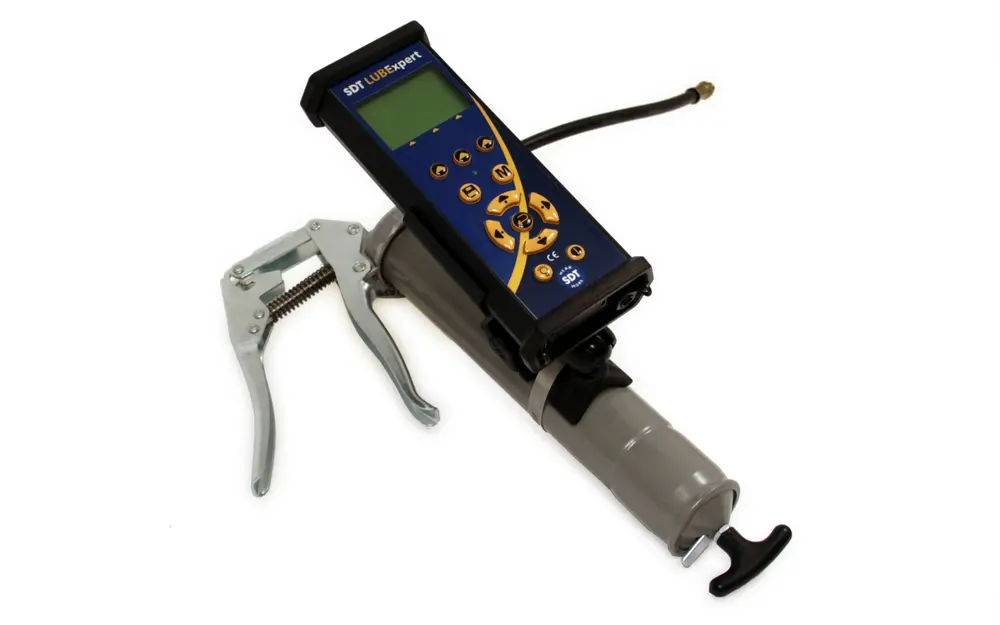
Avantages
Les mesures par ultrasons présentent certains avantages spécifiques qui s'inscrivent dans le cadre de la maintenance conditionnelle et prédictive. Par exemple, elles peuvent être déployées dans pratiquement n'importe quel environnement. Les autres sons audibles qui empêchent généralement les gens d'identifier les problèmes avec leurs oreilles ne sont pas captés par les appareils à ultrasons. Pensez au bruit produit par d'autres machines, la radio, les sons extérieurs, etc. Seuls les sons très aigus du roulement ou d'un autre composant sur lequel la sonde du capteur est fixée sont enregistrés sans pollution sonore inutile. Au cours du processus, chaque roulement est mesuré séparément, ce qui donne une indication claire par composant.
Comme indiqué brièvement plus haut, le dispositif est relativement simple à utiliser. Par conséquent, aucune formation (coûteuse ou longue) n'est nécessaire pour commencer à l'utiliser, ce qui le rend peu contraignant pour les services techniques souvent très occupés. En outre, les mesures sont effectuées en temps réel et peuvent être réalisées lorsque la machine est en marche. De plus, la technologie est relativement bon marché, ce qui constitue un autre avantage lorsqu'un service technique est curieux et souhaite l'essayer pour la première fois.
Enfin, les utilisateurs de la dernière génération d'appareils à ultrasons bénéficient des derniers développements en matière de logiciels et d'analyse des données. Cela signifie que ces appareils sont capables de stocker de grandes quantités de données, par exemple, et de les utiliser pour construire un historique sur base duquel il est possible d'effectuer des analyses de tendances. Enfin, la technologie des ultrasons a fait ses preuves au fil du temps en tant que technologie pratique et surtout fiable dans le contexte de la maintenance conditionnelle et prédictive.
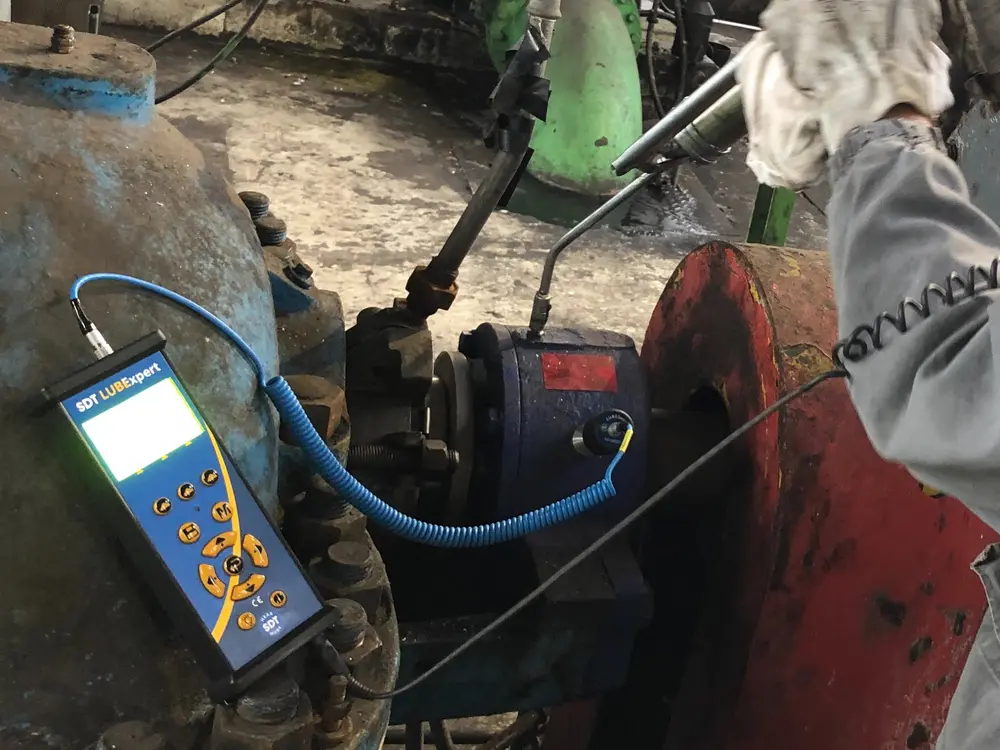
En pratique
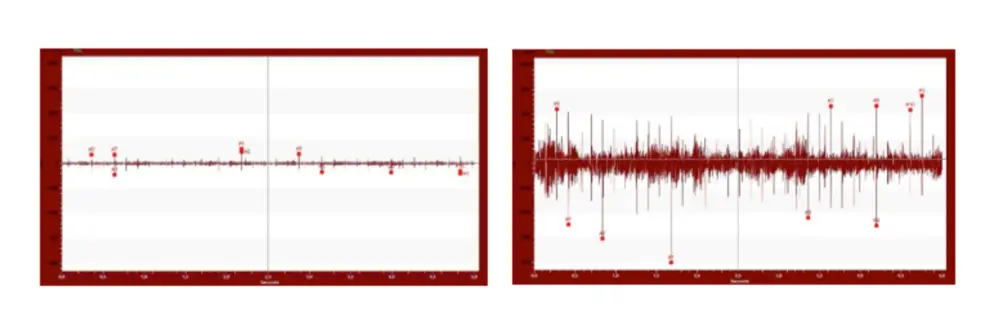
La réalisation de mesures par ultrasons nécessite un appareil à ultrasons proposé par différents fabricants et fournisseurs. Les entreprises qui commencent à effectuer des mesures par ultrasons doivent d'abord réaliser une mesure de référence. Le meilleur point de départ est, bien sûr, un bon roulement qui fournit une valeur - ou une valeur moyenne basée sur plusieurs mesures - que le collaborateur peut utiliser comme référence.
Une fois que l'appareil et les valeurs de référence sont disponibles, l'appareil à ultrasons peut être utilisé de deux manières.
- Inspecter les roulements et identifier les écarts par rapport à la mesure de référence. Ces écarts peuvent faire l'objet d'une évaluation plus poussée ou être utilisés directement pour programmer la maintenance. En général, lorsque l'amplitude d'un roulement dépasse 8 dB et qu'il n'y a pas de différence dans la qualité du bruit au niveau de référence, le roulement doit être lubrifié.
- Déterminer le moment où une quantité suffisante de lubrifiant a été ajoutée. Il s'agit d'une autre application courante utilisée pour éviter la sur-lubrification des roulements en particulier. A cette fin, le collaborateur mesure le niveau de bruit lors de l'ajout de graisse. Le niveau de décibels change et se rapproche de la valeur optimale. Lorsque cette valeur est atteinte, l'employé arrête le graissage. Bien entendu, cela ne s'applique que lorsque le roulement a réellement besoin de lubrifiant. Si les valeurs s'écartent parce que trop de lubrifiant a été ajouté auparavant, les valeurs ne feront qu'augmenter et s'éloigneront de la valeur optimale. L'employé comprendra immédiatement qu'il doit arrêter la lubrification et éventuellement débarrasser le roulement de l'excès de graisse.
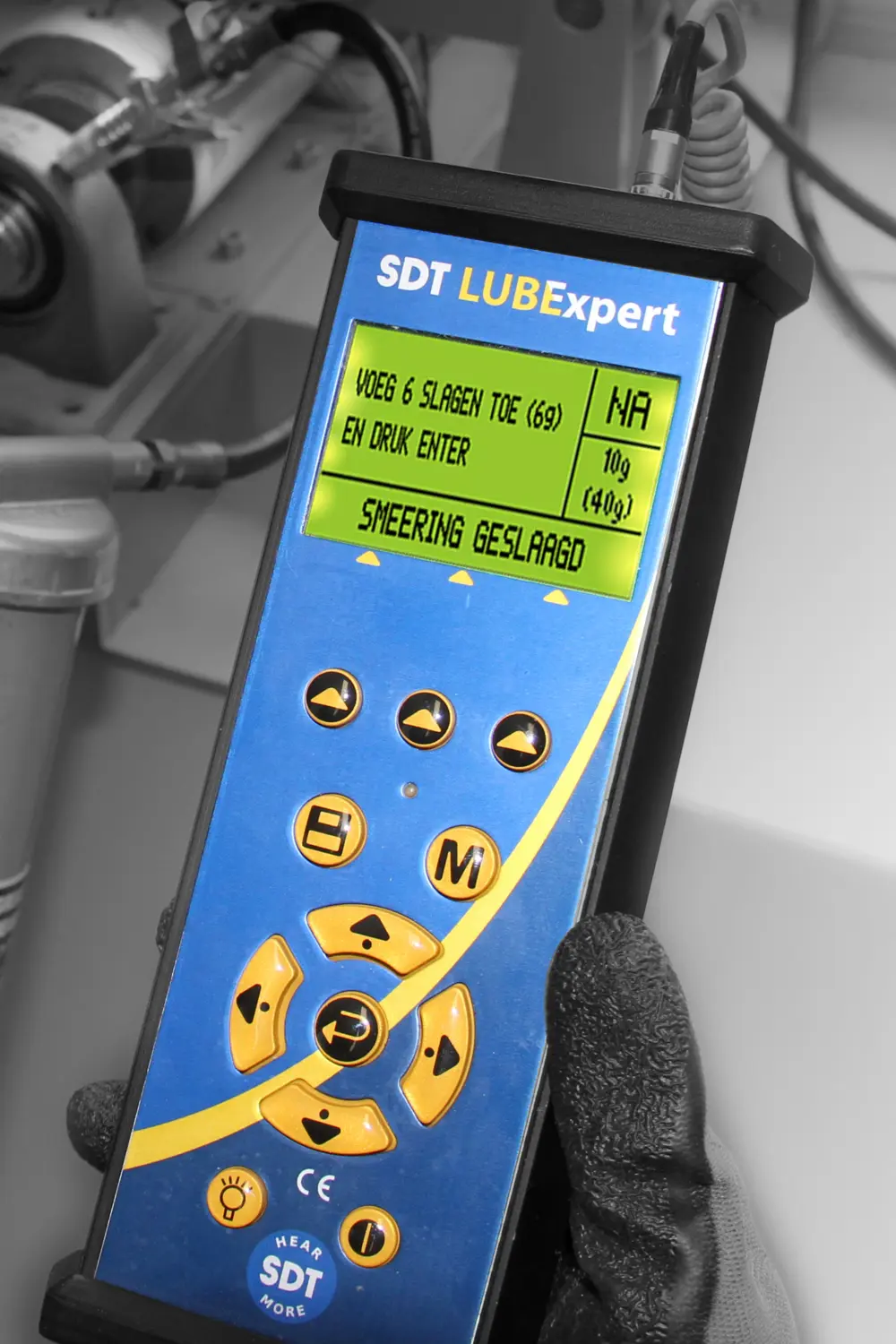
Enregistrement des données
L'utilisation de mesures ultrasoniques pour déterminer la bonne quantité de graisse est pratique et fiable. Pour tirer le meilleur parti de cette technologie, il est conseillé d'enregistrer chaque opération de lubrification sur un composant spécifique, en précisant le moment où elle a eu lieu et la quantité de graisse ajoutée. Avec la génération actuelle de programmes de maintenance et la disponibilité des tablettes, cela ne devrait pas poser de problème.
L'enregistrement de ces données relativement simples permet, entre autres, de déterminer la quantité de graisse nécessaire par roulement et présente également une valeur logistique. En outre, la programmation de la maintenance de la lubrification peut être affinée de manière à ce que la lubrification ne soit pas effectuée trop tôt mais pas non plus trop tard.
Une lubrification excessive peut entraîner une augmentation du frottement et une consommation inutile de graisse
Il y a des avantages dans les deux cas: si les intervalles de lubrification peuvent être allongés sur base des mesures, le service technique économise des heures de travail et des lubrifiants. Si les intervalles de lubrification étaient trop longs et qu'il faut donc lubrifier plus souvent, cela signifie qu'il y a eu un frottement constant et inutile, ce qui réduit la durée de vie des composants et augmente la consommation d'énergie. Une lubrification plus fréquente résout ces inconvénients, ce qui s'accompagne d'avantages en termes de coûts.
Ceux qui souhaitent commencer à effectuer des mesures par ultrasons dans le cadre de la maintenance de la lubrification ont tout intérêt à chercher un fournisseur d'équipement qui soit également disposé à fournir des conseils et une assistance lors de la mise en œuvre. Ainsi, cet élément de la maintenance prédictive peut être mis en place correctement dès le départ et le profit est maximal.
En collaboration avec SDT Ultrasound Solutions et de SKF