Modification des normes de sécurité pour la commande bi-manuelle
disparition de La norme EN 574, modification des normes EN 13857 et EN 349
Nos environnements de production ont beaucoup changé ces dernières années, c'est le moins qu'on puisse dire. Les normes de sécurité correspondantes doivent donc être régulièrement adaptées à cette nouvelle réalité. Récemment, la norme EN 574:2010 concernant les dispositifs de commande bi-manuelle a été remplacée par la norme EN ISO 13851. Par ailleurs, les normes EN 349 et EN ISO 13857 ont été légèrement modifiées.
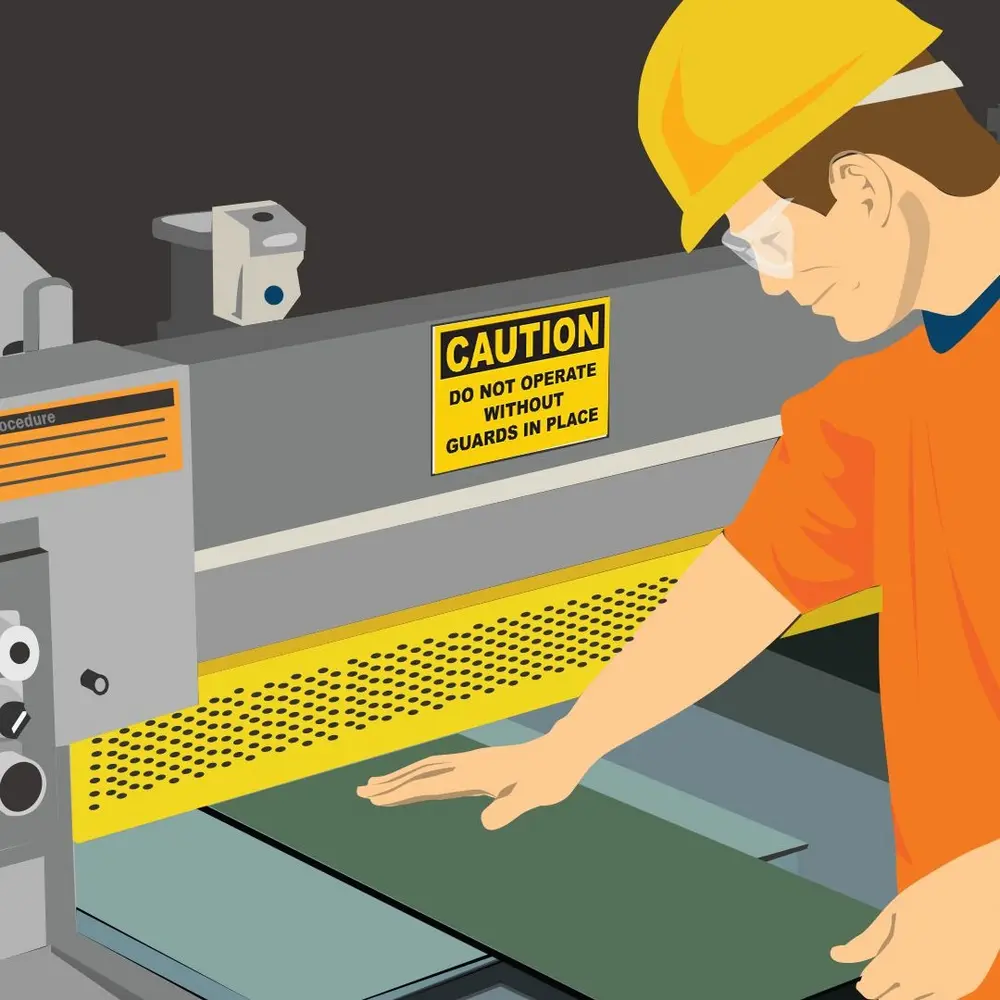
Les petites tâches d'assemblage restent nécessaires
Le fait que ces normes de sécurité concernant la commande bi-manuelle aient été adaptées semble assez étrange à première vue. L'automatisation et la robotisation ne permettent-elles pas de réduire de plus en plus le travail manuel? C'est probablement le cas mais une autre évolution importante est en cours: l'individualisation des biens. Des produits sur mesure, selon des instructions qui peuvent changer à tout moment. Cela entraîne des séries de produits plus petites, difficiles à automatiser à 100%. Les petites tâches d'assemblage, de contrôle et de réparation resteront donc toujours dans nos ateliers et sont de plus en plus souvent intégrées dans le processus plus large: l'employé doit sortir la pièce de la machine, effectuer une tâche sur celle-ci et la replacer dans la chaîne de production pour un traitement ultérieur et/ou l'emballage. En d'autres termes, les risques potentiels sont toujours présents.
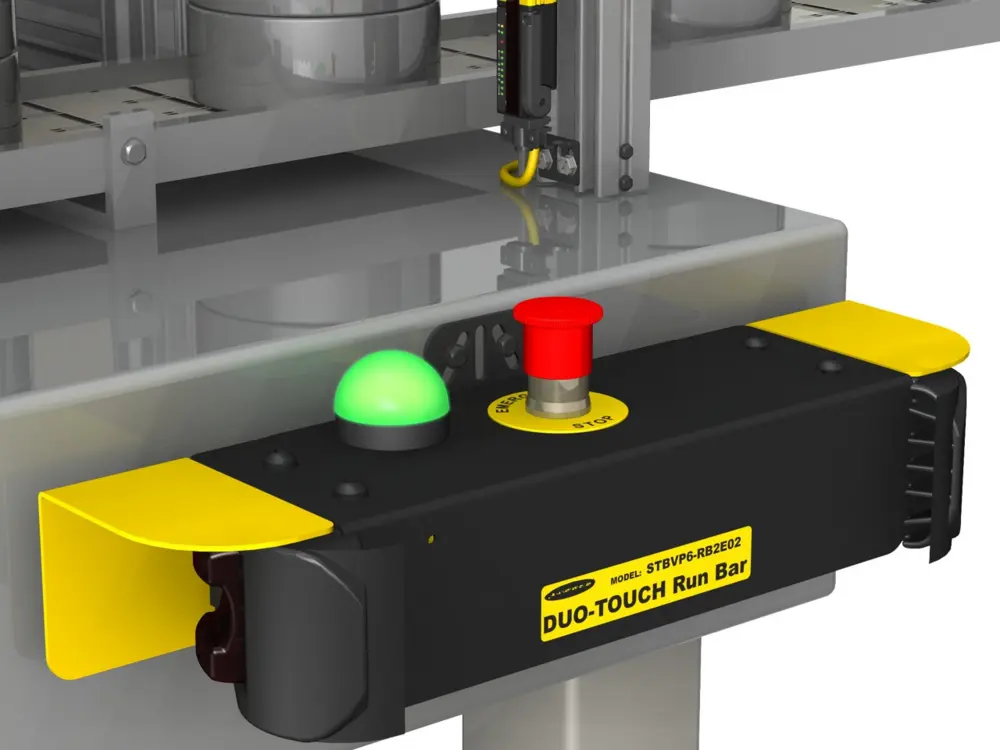
utilité de la commande bi-manuelle
Toute personne effectuant des tâches de montage, de contrôle ou de réparation dans la chaîne de production est confrontée à divers risques, tels que le danger de rester coincé dans la machine ou d'être blessé par l'opération en raison d'une mise hors tension trop tardive ou d'une remise en marche trop rapide. Pour réduire ces risques, la commande bi-manuelle est un bon instrument: la machine ne peut être remise en marche que si l'opérateur appuie sur les deux boutons poussoirs avec les deux mains simultanément et - ce qui est parfois négligé - elle ne fonctionnera que tant que les deux boutons seront enfoncés. C'est une bonne approche en soi mais les risques résiduels ne doivent pas être négligés. Une commande bi-manuelle est principalement sûre pour l'opérateur du poste de travail mais pas pour une personne supplémentaire. La situation fréquente où un technicien vient réparer un défaut au poste de travail et est blessé par la machine ne peut pas être évitée par une commande bi-manuelle.
À cet égard, la norme existante EN 574:2010 était un peu trop limitée. Il était donc nécessaire de passer à d'autres normes afin de garantir la sécurité des hommes et des machines, telles que la célèbre EN ISO 12100. Elle stipule notamment que "toute la zone dangereuse accessible doit être visible depuis le poste de travail de l’opérateur. Faute de quoi, il pourrait mettre en danger par inadvertance une personne entrant dans la zone de danger".
Un peu plus loin, elle précise: "Les ouvertures d’accès à la zone de danger doivent être aussi petites que possible, afin que personne ne puisse atteindre intentionnellement la zone de danger ou trébucher et tomber accidentellement. En principe, l’ouverture d’accès doit être juste assez grande pour permettre d’effectuer l’opération, comme l’insertion et le retrait de pièces. Pour réduire l’ouverture d’accès, il peut être nécessaire d’installer des protections fixes et/ou mobiles".
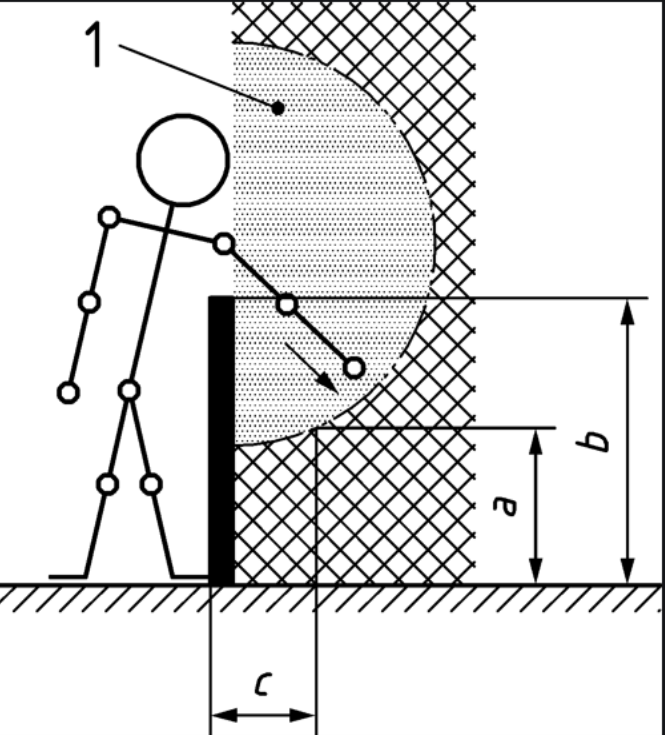
Une barrière de protection trop basse pourrait encore provoquer un contact entre l'homme et la machine. La modification inclut donc également la saisie en hauteur (1) car les robots ont une zone de travail plus élevée que les machines traditionnelles.
Afin de rationaliser davantage les normes de sécurité relatives à la commande bi-manuelle, la norme EN 574:2010 est désormais remplacée par la norme EN ISO 13851. Le chapitre sur les exigences fonctionnelles pour la commande bi-manuelle est le suivant:
"Les boutons doivent être enfoncés simultanément (délai max. 0,5 seconde), et il ne doit pas être possible de redémarrer la fonction, sauf si l’opérateur laisse les deux boutons éteints (commande bi-manuelle de type 3)". Ensuite sont énumérées les exigences supplémentaires en fonction de la norme EN ISO 13849-1, la norme connue pour la sécurité des machines. La norme EN ISO 13851 fait explicitement référence à cette norme. La commande bi-manuelle étant une fonction de sécurité, elle doit fonctionner de manière fiable. C'est pourquoi le niveau de performance PL=c est proposé comme minimum, et même PL=d pour les dispositifs de sécurité de type 3.
Outre cette exigence, deux autres questions importantes se posent. D'abord, il doit être impossible d'activer l'un des deux boutons de manière involontaire. La seconde exigence concerne la distance entre la commande bi-manuelle et le risque: si l'opérateur lâche l'un des boutons, le mouvement dangereux doit s'arrêter suffisamment tôt pour l’empêcher d’atteindre les pièces mobiles et de se blesser. Pour calculer exactement ces distances, il faut se baser sur la norme EN ISO 138555 et vérifier avec des essais.
La sécurité seule ne suffit plus
En pratique, la modification de la norme EN 574:2010 a peu d'effet sur le dispositif de sécurité proprement dit. La principale différence réside dans le contrôle de la fonction de sécurité. C'était également le cas auparavant pour les normes dites B2, qui régissaient les dispositifs de sécurité tels que les barrières immatérielles de sécurité, les arrêts d'urgence, les contrôleurs de pression et la surveillance optoélectronique. Pour ces dispositifs également, une exigence supplémentaire de vérification et de validation a été introduite au fil des ans. Cela garantit que les composants de sécurité fonctionnent conformément aux exigences de la norme (vérification) et qu'ils fonctionnent correctement dans la pratique (validation).
Cette exigence supplémentaire est donc également introduite pour la commande bi-manuelle, bien que dans la pratique cela s'applique principalement aux constructeurs de machines. Ils doivent également étoffer les informations destinées à l'utilisateur avec, entre autres, un manuel d'installation et de maintenance amélioré. L'objectif de ce dernier est bien sûr de garantir un fonctionnement sûr dans le temps. Ce dernier point semble être un problème dans la pratique sur de nombreux lieux de travail: les entreprises n'en savent pas assez sur les exigences de maintenance, les dispositifs ne sont pas suffisamment testés ou il y a des modifications de la machine qui rendent le dispositif de sécurité inadéquat.
La norme EN 349 devient la norme EN ISO 13854
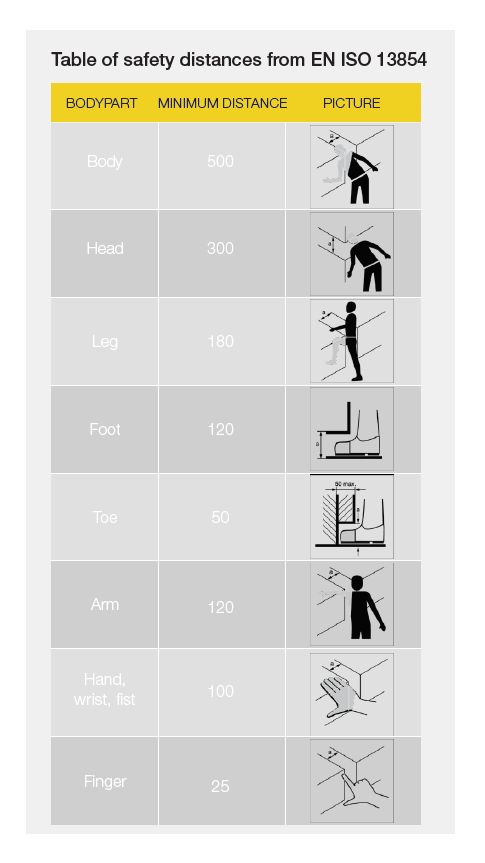
On note un changement plutôt administratif dans la norme EN 349, qui est enfin harmonisée avec la norme EN ISO 13854 concernant les distances minimales pour prévenir les risques d'écrasement de parties du corps humain. Cette harmonisation n'a pas de conséquences pratiques sur le lieu de travail.
Mais la norme EN ISO 13857 a été modifiée
Les normes de sécurité actuelles ne sont guère susceptibles de changer et il n'y a pas de bouleversements révolutionnaires à attendre dans un avenir proche. Les modifications qui sont apportées aujourd'hui aux normes existantes sont principalement des modifications brèves. Elles sont effectuées parce que les normes existantes présentent de petites lacunes dans la pratique ou parce que de nouvelles situations compromettent les normes de sécurité.
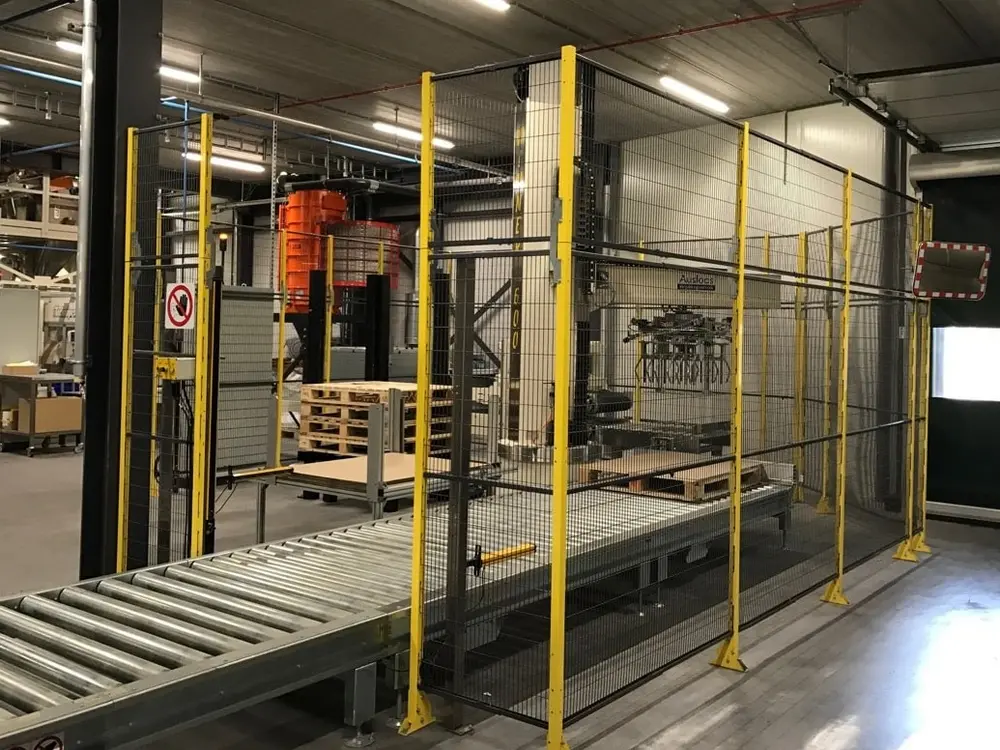
Une modification de la norme EN ISO 13857 en est un bon exemple. Cette norme a été créée pour empêcher les membres supérieurs et inférieurs d’atteindre les zones dangereuses en énumérant les distances de sécurité minimales. Cette norme était principalement basée sur les dangers d'une machine traditionnelle. Les distances de sécurité ont donc été fixées dans ce sens. L'émergence des robots a été beaucoup moins prise en compte, si bien que les distances existantes ne tenaient pas suffisamment compte de la 'réalité des robots', notamment la portée en hauteur beaucoup plus importante de ces machines. Ils atteignent parfois des hauteurs bien supérieures à celles des barrières de protection standard de 2 ou 2,5 mètres. Dans la norme modifiée, la zone de risque a donc été ajustée sur base d'un éventuel mouvement de saisie vers le haut de l'opérateur, ce qui nécessitera dans certains cas un ajustement de la hauteur de la barrière de protection. Lorsque la hauteur maximale de la clôture est atteinte, il faudra vérifier si la marge de distance minimale de 120 mm a été atteinte.
Basé sur le livre blanc "Nouvelles normes pour définir les principes de base des postes de travail manuels" d'Axelent.