Les systèmes MES doivent mener à une utilisation plus efficace des machines
Contrôle et optimisation de la production en temps réel grâce aux données
L'industrie 4.0 tourne autour de la connexion et de la communication entre les machines et divers autres systèmes logiciels de l'entreprise. Les Manufacturing Execution Systems (MES) jouent un rôle important à cet égard, car ils constituent le lien entre la réalité concrète des machines et le côté administratif d'une entreprise. Ainsi, l'optimisation des processus peut se faire sur base de données réalistes et la production est contrôlée en temps réel à partir du système ERP.

Traçabilité dans l'industrie manufacturière
Il y a quelques années, les systèmes MES étaient réservés aux grandes entreprises. Il en va de même pour les logiciels de gestion intégrés (ERP). Au départ, ces systèmes étaient surtout utilisés dans des secteurs où la traçabilité était importante, comme l'industrie aérospatiale, l'industrie alimentaire et l'industrie pharmaceutique.
Toutefois, ces dernières années, les systèmes MES ont également trouvé leur place dans l'industrie manufacturière. Les systèmes ERP et MES se sont démocratisés et sont désormais accessibles aux PME manufacturières.
Cette tendance est motivée, d'une part, par les lois et réglementations exigeant une plus grande traçabilité et, d'autre part, par l'évolution des logiciels. La programmation low-code, les interfaces plus universelles pour l'échange de données et les techniques de machine learning sont à l'origine de cette accélération. Cela attire également de nouveaux acteurs sur le marché des MES, dont certains sont déjà actifs dans les ateliers de production, mais nous y reviendrons plus tard.
Des réglementations environnementales plus strictes, notamment en ce qui concerne les émissions de CO2, renforceront encore cette croissance, car les équipementiers de la chaîne d'approvisionnement commencent à demander plus de détails sur les émissions de CO2 provenant de la production de composants.
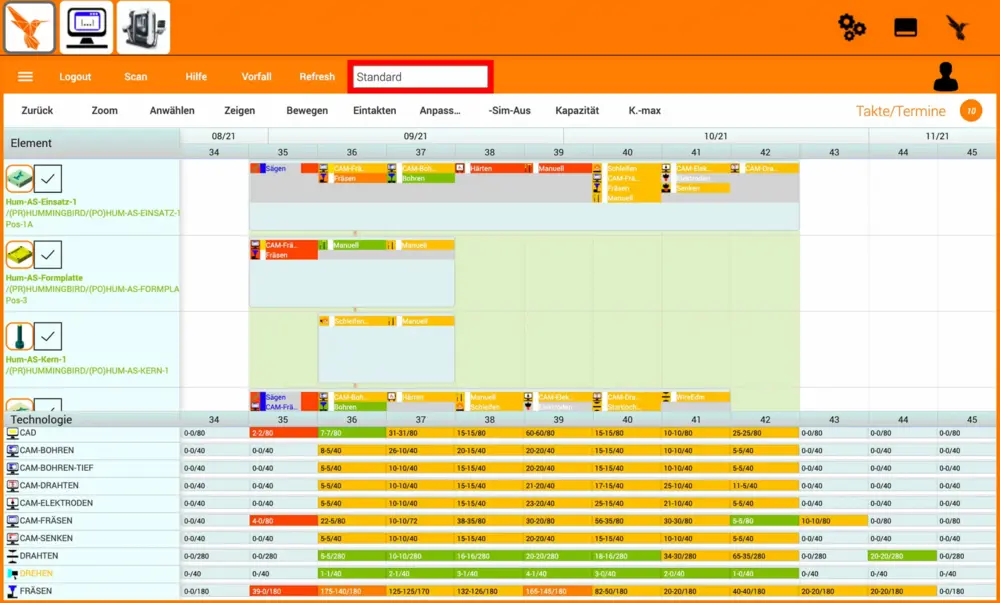
Le système MES en tant que couche intermédiaire
Dans la norme ISA-95, vieille de plus de 25 ans, un système MES est défini comme 'un système de gestion de la production'. Il se situe donc entre le système ERP (planification et logistique, niveau 4) et le contrôle des processus (niveaux inférieurs).
Le système ERP contient des données telles que les commandes des clients, les devis, les délais de livraison, la disponibilité des matériaux et des outils, etc. Le système MES charge ces données et s'attelle à la planification de la production et, plus important encore, continue à surveiller la production et à renvoyer ces données au système ERP. Cela permet de savoir en temps réel où la production se situe par rapport aux dates de livraison convenues.
Il est ainsi possible de détecter rapidement les goulets d'étranglement, dus par exemple à des arrêts machines imprévus ou à des outils manquants, et de prendre les mesures qui s'imposent. Cette action peut consister à commander automatiquement des outils ou des matériaux, à transférer la production sur d'autres machines ou à travailler avec les clients à un stade précoce afin d'ajuster les calendriers.
L'industrie 4.0 conduit à la décentralisation; les connaissances sous forme de solutions numériques sont disponibles à un niveau inférieur. Les systèmes MES sont un 'facilitateur' pour la production décentralisée
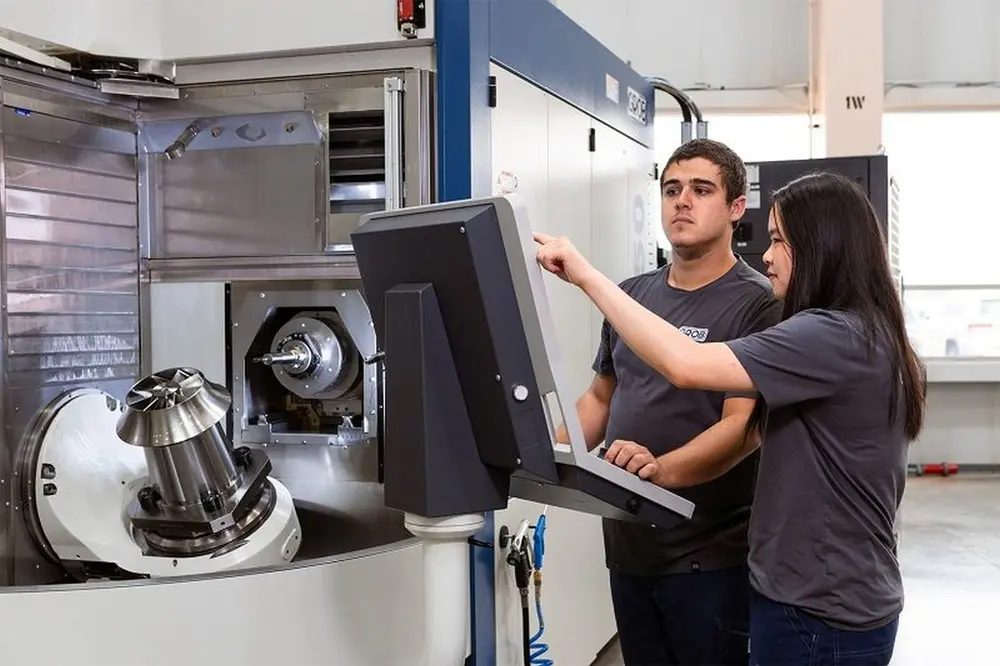
Importance des interfaces
Le fait que les systèmes MES aient été développés plus tardivement que les systèmes ERP a une raison évidente: les usines intelligentes dépendent des données provenant des machines. Il peut s'agir d'informations lues directement à partir des commandes de la machine ou de données provenant de ce que l'on appelle les capteurs IIoT (Industrial Internet of Things).
Un système MES est alimenté d'une part par des données provenant du système ERP (ou PLM) et d'autre part par des données provenant de la production. Ce dernier point a longtemps empêché une percée des systèmes MES vers l'industrie manufacturière. Ce n'est qu'avec l'arrivée de nouvelles interfaces, telles que la MTConnect américaine et, plus récemment, l'umati allemande/européenne, qu'il est devenu plus facile d'extraire et d'utiliser les données provenant du hardware. Cette étape était nécessaire pour rendre les systèmes MES plus applicables dans les PME.
Dans une application simple, ces données sont renvoyées au système ERP et utilisées pour ajuster la production. Toutefois, ces informations permettent également de mieux comprendre l'utilisation efficace des machines. Le système MES recueille des données pour savoir si la broche d'un centre d'usinage à 5 axes tourne ou non, enregistre le temps qu'un opérateur CNC passe à régler la machine pour une nouvelle tâche et enregistre les pannes de la machine. Toutes ces données sont présentées dans des dashboards clairs.
Un tel dashboard - ou, de plus en plus souvent, une application - permet au chef d'atelier de se faire une idée de la manière dont la production se déroule actuellement et montre où se situent les domaines d'amélioration les plus prometteurs. Par exemple, la comparaison entre les temps de réglage et les temps calculés, ou encore les causes les plus fréquentes des pannes de machines. Ou encore les causes les plus courantes des pannes de machines. Au final, les décisions prises sur la base de ces données améliorent le taux d'utilisation des machines.
Un autre avantage est la possibilité de réduire les stocks car la planification utilise les données ERP. L'un des défis que doivent relever les développeurs de systèmes MES consiste à désenclaver des chaînes de valeur entières, non seulement au sein d'une entreprise, mais aussi les données de partenaires externes de la chaîne. Les données des différents partenaires de la chaîne devraient ainsi devenir plus transparentes pour toutes les parties concernées. Dans cette intégration horizontale, le cloud computing jouera un rôle essentiel.
L'un des défis pour les développeurs de systèmes MES est de savoir comment désenclaver des chaînes de valeur entières, non seulement au sein d'une entreprise, mais aussi les données de partenaires externes de la chaîne
Intelligence artificielle
Actuellement, l'essor du Machine Learning (ML) et, dans les années à venir, de l'intelligence artificielle (IA) simplifie encore l'utilisation des systèmes MES et facilite l'analyse de toutes les données et la prise de décisions. Cette évolution résultera notamment du développement rapide de ce que l'on appelle les Large Language Models (LLM). Tout comme on demande déjà des informations en tapant un prompt dans ChatGPT, dans un avenir proche, l'intelligence artificielle pourrait être programmée en énonçant simplement en mots ce que que l'on veut.
Certains affirment que le langage deviendra la principale interface logicielle à l'avenir. Il ne sera plus nécessaire de faire appel à un expert en intelligence artificielle pour créer ou personnaliser une application particulière. Pour les PME en particulier, cela signifie que beaucoup plus d'outils de contrôle et d'analyse deviendront accessibles, non seulement en termes d'investissement, mais surtout en termes d'utilisation. Un système MES fournit à la fois une vue d'ensemble de ces données et les ramène à un niveau supérieur pour analyse.
Dans une étude récente, des chercheurs de l'université de Pannonie en Hongrie distinguent six étapes de l'industrie 4.0. Les deux premières étapes impliquent l'informatisation et la connectivité au niveau de la machine individuelle. À ce niveau, le MES ne joue pas encore de rôle. La troisième étape consiste à rendre visible ce qui se passe dans la production pour ensuite créer une transparence totale à travers la quatrième étape. Le MES entre en scène à partir de la troisième étape.
On atteint alors les deux dernières étapes où l'amélioration est centrale. D'abord la maintenance prédictive, puis, dernière étape de l'industrie 4.0, la capacité d'adaptation de la production pour s'adapter instantanément à des conditions changeantes. C'est dans cette phase qu'un système MES peut être pleinement utilisé.
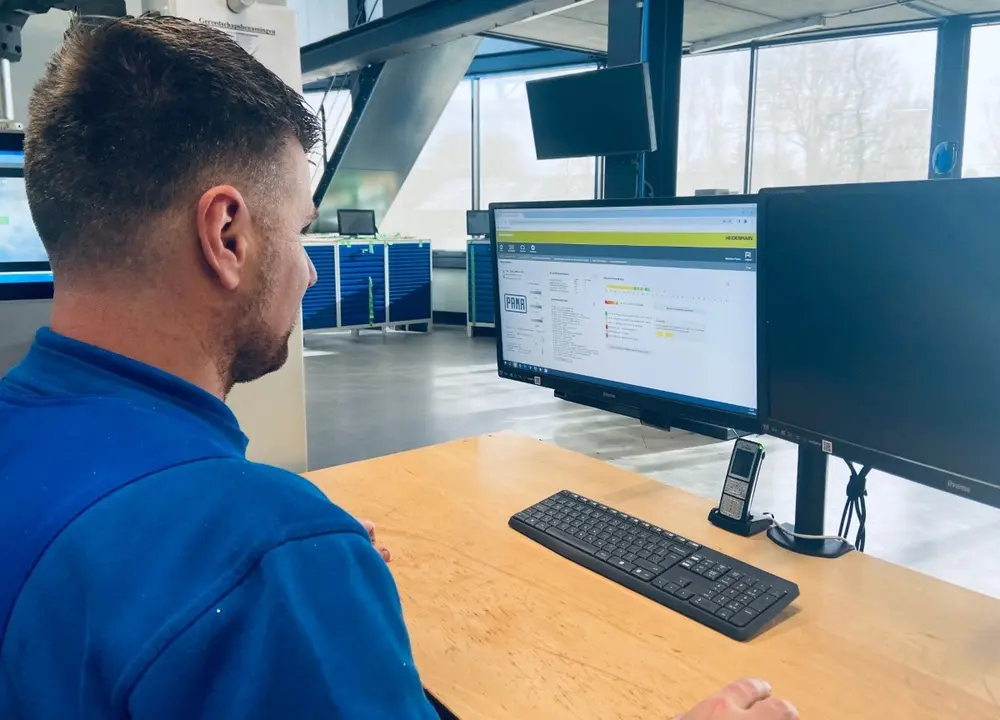
Nouveaux fournisseurs de systèmes MES
Lorsqu'on examine les fournisseurs de systèmes MES, on constate une évolution intéressante. Alors qu'auparavant, ce sont surtout les développeurs de logiciels spécialisés qui proposaient des systèmes MES, ces dernières années, les constructeurs de machines et les développeurs de FAO, entre autres, se sont également lancés sur ce marché. Ils constatent que la demande augmente, que les interfaces entre les machines et les logiciels facilitent leur utilisation et ils ont souvent déjà un point d'entrée avec l'utilisateur final, en l'occurrence l'entreprise métallurgique. Certains hébergent les activités MES dans une entreprise distincte, tandis que d'autres les intègrent dans des solutions existantes.
L'évolution des systèmes de surveillance des machines à commande numérique vers des systèmes MES est relativement récente. Au départ, les premiers systèmes étaient conçus pour obtenir un aperçu du déploiement efficace d'une machine. Toutefois, les fabricants de machines intègrent progressivement de nouvelles fonctionnalités dans leurs systèmes de surveillance, qui permettent également la planification et même un lien direct avec un système ERP, par exemple. Ils ne se contentent donc pas de lire l'efficacité d'une machine au niveau individuel.
Les fabricants de machines ne sont pas les seuls à travailler sur ce développement. On voit également apparaître des fournisseurs de solutions qui se présentent comme une solution indépendante de la machine. Ce point est toutefois dépassé, car les fabricants de machines se sont rendu compte qu'une solution spécifique à leurs machines n'est pas une solution viable dans la pratique. Rares sont les entreprises métallurgiques qui n'ont qu'une seule marque de machine dans leur production.
L'objectif ultime de tout ceci est de parvenir à un processus d'amélioration continue.
L'objectif ultime de tout ceci est de parvenir à un processus d'amélioration continue