QUE FAIRE EN CAS DE VARNISH?
Contrer la problematique avec des mesures modernes
Varnish: un phénomène autrefois inconnu, mais aujourd’hui un gros souci pour de nombreux utilisateurs d’installations hydrauliques, de compresseurs & de turbines. Il s’agit d’une couche poisseuse brun-noir se déposant sur les éléments d’installation et altérant ainsi leur fiabilité et leur précision. Des recherches ont entre-temps révélé les causes et constitué la base du développement d’une unité de filtration intégrant un filtre en profondeur comme un filtre ionique. Cela n’empêche certes pas l’apparition des particules causant le varnish, mais permet d’atteindre un équilibre maîtrisable.
BRUN ET POISSEUX
Cause d’obstructions
Varnish est le terme collectif anglais désignant une couche de vernis brune brillante molle ou dure se déposant sur les surfaces dans les systèmes hydrauliques et à huile de lubrification. Cette couche poisseuse peut générer des obstructions ou l’adhérence de composants. La machine ou l’installation perd ainsi sa fiabilité et sa précision, et fournit de mauvais temps de réaction. Cela favorise aussi un vieillissement prématuré du batch d’huile et, dans le pire des cas, une défaillance du système complet avec tous les coûts qui s’ensuivent.
Cause de défaillances de turbines à gaz
Des recherches ont démontré que le varnish était même l’une des principales causes de la défaillance de grosses turbines à gaz. Un rapport de 2005 de General Electric indiquait que des mesures étaient certes déjà recommandées à cette époque pour éliminer le varnish des systèmes, mais que la cause finale n’était pas encore connue. Cela revenait à ‘mettre un emplâtre sur une jambe de bois’. Les coûts liés aux pannes et défaillances dues au varnish étant énormes, le nouveau phénomène a fait l’objet de recherches intensives les années suivantes. Cela s’est soldé vers 2008 par une compréhension complète de l’apparition du varnish, constituant une bonne base pour le développement de solutions adéquates.
COMMENT LE VARNISH APPARAIT-IL?
Soluble ou non?
La couche de vernis poisseuse et brun-noir reconnaissable consiste en fait en particules résultant de la dégradation de l’huile. La dégradation est la conséquence de réactions chimiques par oxydation au niveau de l’huile, transformant cette huile en molécules organiques avec une masse moléculaire élevée. Ces particules sont tout d’abord dissoutes (soluble) dans l’huile, où elles causent en principe encore peu de problèmes. Quand le point de saturation de l’huile est cependant atteint, les particules sortent de la solution (insoluble), s’agglutinent et se déposent sur les surfaces disponibles, souvent plus froides. Contrairement à la formation de produits de dégradation – une réaction irréversible, les derniers processus sont de nature physique et donc bien réversibles.
Maîtriser les produits de dégradation
Tout ceci indique que le dépôt final des particules (le varnish proprement dit) est le résultat final d’un processus amorcé bien plus tôt. Il n’est pas possible d’empêcher ce processus, vu que l’huile vieillira toujours; l’apparition de particules de dégradation est donc un fait. La solution ne réside dès lors pas dans la tentative d’arrêter ce processus, mais dans la maîtrise des produits de dégradation dans le système. Cela signifie tout d’abord tenter de ralentir autant que possible le vieillissement de l’huile, afin de minimiser la quantité de produits de dégradation. Il s’agit également d’éliminer au plus vite les particules apparaissantes. Si le système de filtration nécessaire pour cela est en mesure d’éviter que le point de saturation de l’huile soit atteint, il ne peut jamais y avoir non plus de retombées de varnish libre (insoluble) dans un système.
CAUSES DE DEGRADATION
Groupes d’huile de base
Une raison majeure pour laquelle les entreprises sont plus confrontées au varnish qu’avant ces dernières années, réside dans le développement de nouvelles huiles de base. Le premier groupe d’huiles (Groupe I) était constitué de quatre composants, parmi lesquels une importante part d’aromates. Ces aromates sont relativement agressifs et donc indésirables. Dans la génération suivante d’huiles (Groupes II et III), on est parvenu à éliminer ces aromates. Ces groupes étaient ainsi plus consistants et plus purs. Les résultats positifs de ces nouvelles huiles ont encouragé les scientifiques à rendre les huiles encore plus pures, ce qui a donné lieu à un Groupe IV d’huiles de base uniquement composé de composants paraffineux.
Inconvénients
Bien que les avantages de ce nouveau groupe soient évidents – comme une longévité accrue, on note aussi de nouveaux inconvénients. En raison de l’absence de particules polaires dans ce groupe IV, la conductivité de l’huile est p.ex. bien plus faible. Des charges électrostatiques apparaissent, de ce fait, plus vite. Cela génère non seulement des brûlures dans les éléments de filtration (un système peut même ‘crépiter’ à la suite des nombreuses décharges), mais aussi de l’huile localement brûlée – en fait rapidement oxydée – et ainsi un grand nombre de produits de dégradation dans l’huile. Une solution pour réduire le nombre de décharges consiste notamment à travailler avec des éléments de filtration antistatiques et à maintenir (si possible) les vitesses de l’huile par le filtre relativement réduites.
Facteurs environnementaux
Outre la nouvelle huile de base, d’autres facteurs (environnementaux) accélèrent la décomposition de l’huile, comme la présence d’eau, d’air et de particules de saleté (surtout de métaux), en combinaison avec des pressions élevées et des températures variant fortement (stress thermique). Ce sont en fait tous des facteurs facilitant la réaction de l’huile avec l’oxygène et accélérant ainsi sa dégradation. Les températures et pressions élevées impliquent que la dégradation de l’huile survienne surtout dans le système et p.ex. pas dans le réservoir à huile. Les hot spots sont en particulier souvent des causes invisibles et inattendues d’un processus de dégradation accéléré. Sous l’effet de températures et pressions plus élevées, plus de varnish peut, en outre, se dissoudre dans l’huile (une température plus élevée augmente le point de saturation), ce qui cause finalement des problèmes quand le système est coupé, et que la température et la pression diminuent ou quand l’huile se retrouve à des endroits plus froids (p.ex. dans les servovalves). Dans ces situations, le point de saturation baisse. De ce fait, les produits de dégradation sortent ‘soudainement’ de l’huile en varnish avec tout ce qui s’ensuit.
RECONNAITRE LE VARNISH
Potentiel de varnish
Quand le varnish a formé une couche poisseuse, il faut peu de discussions pour constater le problème. Il est plus intéressant de découvrir combien de particules de dégradation sont dissoutes dans l’huile; c’est ce que nous appelons le taux de soluble varnish dans l’huile ou le potentiel de varnish. Cela permet, en effet, de déterminer quel est le risque que ces particules se déposent prochainement sous la forme de varnish, et également de contrôler si des mesures spécifiques ont ou non l’effet escompté.
Test MPC
Un des tests pour le déterminer est le test MPC, ou Membrane Patch Colorimetry. Il s’agit ici d’un test relativement simple qu’il faut exécuter comme le décrit l’organisation de standardisation américaine ASTM (American Society for Testing and Materials) dans l’ASTM-D7843-16. Sur la base du changement de couleur et de la profondeur de couleur d’une membrane d’analyse de 0,45 µm, ce test détermine la sensibilité au varnish d’un système à ce moment. La valeur de mesure est un nombre entre 0 (pas de particules) et 100 (membrane complètement noire) et la valeur d’alarme se situe entre 30 – 40. Toute valeur inférieure à 15 signifie qu’aucun problème n’est attendu, tandis que des valeurs à partir de 41 indiquent que des mesures doivent être prises directement.
Indications de temps
Pour obtenir un résultat fiable, il est essentiel que les temps indiqués dans la description du test soient respectés avec précision. Ces temps étant relativement longs (d’abord 24 heures dans l’étuveur, puis 68-72 heures de repos dans un espace sombre), une partie des laboratoires n’est pas prête à exécuter ces tests exactement conformément à la norme. Cela peut donner lieu à des résultats d’analyse très variables ou anormaux. Conformément à l’ASTM-D7843-16, ces temps doivent être indiqués avec les résultats d’analyse et il est donc conseillé de se méfier de tout rapport dans lequel ces valeurs ne sont pas données.
COMPTEURS DE PARTICULES
Les compteurs de particules (Automatic Particle Counters ou APC) fonctionnent sur la base de l'obscurcissement de la lumière. Un faisceau laser est projeté à travers un flux d'huile dans un capteur sur un photodétecteur. Les particules dans l'huile hydraulique ou l'huile lubrifiante bloqueront le faisceau et projetteront une ombre sur le photodétecteur. Plus la particule est grande, plus l'ombre est grande et plus le signal mV (millivolt) qui sort du détecteur est élevé. L'étalonnage est basé sur la relation entre les tailles de particules connues du fluide d'étalonnage (entre 4 et 50 µm(c) et les valeurs en mV (voir ISO 11171: 2016).
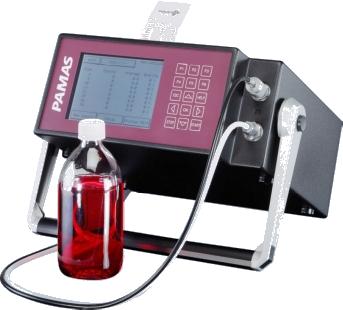
Les APC existent en deux variantes: cellules de mesure in situ (aussi nommés ‘particle monitors’) d’une part et compteurs de particules avec capteurs volumétriques d’autre part. Alors que le premier type (et donc le flux d’huile) n'éclaire la cellule de mesure que pour une certaine partie, la cellule de mesure volumétrique assure l'éclairage intégral. Cela signifie que chaque particule entrant dans le capteur est mesurée en taille et comptée individuellement, ce qui n’est pas le cas pour les cellules de mesure in situ. En fonction du pourcentage d’éclairage, les particules sont mesurées ici comme plus petites ou elles ne sont même pas du tout comptées.
Le varnish ne pose pas de problème pour les compteurs de particules, tant que la quantité de particules solubles et insolubles n'est pas excessive. La taille de ces particules carbonisées est en principe inférieure à 4 µm(c) et, dans ce cas, n'affectera pas les classes de contamination obtenues (situées à partir de 4 µm(c) et plus, selon ISO 4406, SAE AS4059). Le comptage sera correct tant que le capteur est capable de compenser l’absorption de l’arrière-plan. Ce n'est que lorsque l’absorption est trop élevée et que le passage de la lumière à travers l'huile devient insuffisant que la disposition des particules avec les capteurs in situ et volumétriques échoue. Ceci peut être exprimé par un signal d'alarme basé sur la défaillance du capteur ou l'obtention de mesures non reproductibles.
RESOUDRE!
Et enfin, les mesures à prendre pour résister à la problématique du varnish. Comme nous l’avons dit, l’apparition de varnish est un processus physique et donc réversible. Cela signifie que l’élimination des particules de saleté dissoutes de l’huile laisse au varnish flottant et même déposé la place pour se dissoudre à nouveau. Ces particules peuvent ensuite aussi être éliminées. Après cette étape de nettoyage, il faut atteindre un équilibre. Ici, la capacité des filtres utilisés doit être suffisamment grande pour éliminer les particules de dégradation apparaissant sous forme dissoute de l’huile. Pour les installations critiques comme les turbines et les compresseurs, il reste judicieux d’exécuter tous les trois mois un test MPC afin de continuer de contrôler la sensibilité au varnish. Cela contribue non seulement à éviter réellement le varnish, mais constitue aussi une excellente indication de problèmes ailleurs en cas de valeurs augmentant soudainement. P.ex. une usure excessive entraînant le dégagement de particules de métal supplémentaires et l’apparition de hot spots éventuels, une fuite donnant lieu à l’infiltration d’eau ou d’air dans le système, etc.
ELIMINER LE PRODUIT DE DEGRADATION
Filtres en profondeur & filtres ioniques
Les solutions disponibles finalement à même d’éliminer les particules dissoutes de l’huile peuvent être réparties en deux catégories: les filtres en profondeur éliminant de l’huile les particules déjà sorties de la phase dissoute à cause du dépassement du point de saturation et les filtres ioniques éliminant les particules dissoutes. Les deux filtres différents sont combinés dans le système de filtration. Dans un système ‘sain’, on place d’abord le filtre ionique, et ensuite le filtre en profondeur. Le filtre ionique débarrasse l’huile des particules dissoutes, tandis que le filtre en profondeur sert de mesure de précaution supplémentaire pour éliminer la boue d’huile se formant tout de même éventuellement – p.ex. à la suite d’une calamité.
Chronologie
Dans le cas de systèmes très encrassés – ce qui ressort de valeurs MPC, p.ex. supérieures à 50, le plus gros de la saleté sera d’abord éliminé avec un filtre en profondeur et ce n’est qu’ensuite qu’un filtre ionique sera utilisé. L’ordre dans lequel l’huile passe par les filtres, reste toutefois: d’abord le filtre ionique, puis le filtre en profondeur. Dans la pratique, il faudra dans 80% des cas 3-4 mois à un système encrassé pour être à nouveau propre. Dans 20% des cas, cette période est de cinq à six mois et il ne faut pas deux, mais trois jeux de filtres. Au cours de la phase stable, un changement annuel des éléments de filtration suffit.
Toujours à température de service
Enfin: l’huile est toujours filtrée à la température de service. Si les particules sont ramenées à un niveau suffisamment bas lors de cette phase, du varnish ne se déposera plus non plus sur les surfaces lors de la phase de refroidissement et d’arrêt.
CONCLUSION
Tester la sensibilité au varnish des systèmes indique dans quelle mesure un système est encrassé. Sur la base des valeurs, des mesures doivent être prises pour nettoyer le système et le garder ensuite propre. Des exemples dans de gros power plants en Amérique démontrent que ces mesures permettent de réaliser des économies pouvant atteindre annuellement des millions de dollars. Mais aux Pays-Bas aussi, les systèmes ont entre-temps largement fait leurs preuves. Et ne pensez pas: 'Je veux bien le croire, c’est quand même l’assurance qui paie …'. Ces parties mentionnent aujourd’hui en petites lettres que le propriétaire est obligé de garder divers paramètres d’analyse comme le degré de propreté de l’huile, la teneur en eau, la valeur MPC et la valeur TAN (acidité) au niveau souhaité. Sinon, la compagnie d’assurances n’a plus aucun devoir de payer …