Restwarmte winnen uit corrosief rookgas
Kunststof HeatMatrix technologie verhoogt energie-efficientie
De procesindustrie kent veel energie-intensieve processen. Ongeveer 10% van de primaire energie gaat verloren via de schoorsteen als restwarmte. Tot nu toe werden deze warmteverliezen door rookgas als onoverkomelijk beschouwd, aangezien verdere warmteterugwinning zou leiden tot zuurcorrosie en alle operationele problemen die daarmee gepaard gaan. HeatMatrix Group ontwikkelde een innovatieve op polymeer gebaseerde warmte-uitwisselingstechnologie die warmteterugwinning uit corrosieve of vervuilende rook- en uitlaatgassen mogelijk maakt. In dit artikel worden eerst de uitdagingen besproken om vervolgens in te gaan op deze innovatie die energieterugwinning tot temperaturen onder het zuurdauwpunt mogelijk maakt.
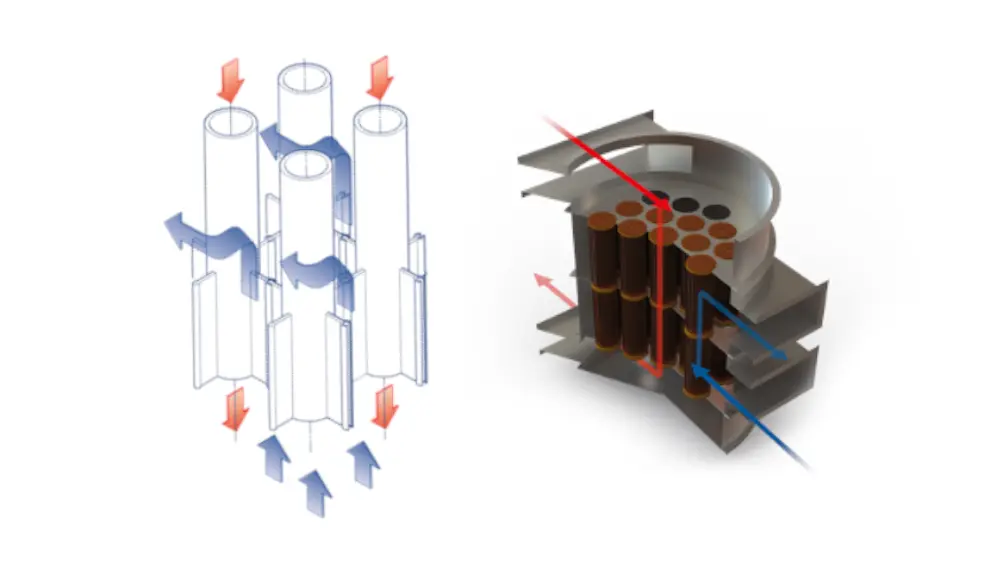
Probleem met warmteterugwinning uit corrosief rookgas
In de industrie wordt een grote variëteit aan brandstoffen verbrand in thermische processen, van aardgas, afgas en LPG tot nafta en stookolie. De meeste van deze brandstoffen bevatten zwavelcomponenten, die omgezet worden naar SOx gedurende verbranding. De meest gevormde component is SO2, maar een gedeelte, typisch 2 tot 4% wordt omgezet in SO3. Wanneer het rookgas onder het zuurdauwpunt (ZDP) komt, reageert SO3 met H2O in een condensatiereactie tot zwavelzuur:
SO3 (g) + H2O (g) → H2SO4 (l)
Het zuur dauwpunt hangt af van de aanwezige concentraties van de reactanten in het rookgas. In het algemeen ligt het zuurdauwpunt tussen de 100-150 ˚C. Figuur 1 laat de relatie zien tussen het ZDP en de SO2-concentratie, berekend met een typische H2O-concentratie van 15 vol% en uitgewerkt aan de hand van verschillende correlaties uit de literatuur. Het gevormde zwavelzuur is zeer corrosief en tast metalen oppervlakten van installaties aan. Bijvoorbeeld op koude oppervlaktes bij de luchtinlaat in luchtvoorverwarmers (LUVO), waar de lokale temperatuur onder het ZDP komt en er zwavelzuurcondensatie plaatsvindt. Dit resulteert in snelle corrosie met als gevolg een lekkende warmtewisselaar. Een lekke wisselaar resulteert in verdere verlaging van de efficiëntie van de warmtewisselaar en verhoging van het elektriciteitsverbruik van de verbrandingsluchtventilator. Wanneer deze ventilator zijn maximumvermogen heeft bereikt, kan het zelfs productieverlaging tot gevolg hebben. Om dit te voorkomen wordt er beperkt warmte teruggewonnen uit rookgas (tot een temperatuur ruim boven het condensatiepunt). Hierdoor is de energie-efficiency niet zo hoog als hij zou kunnen zijn.
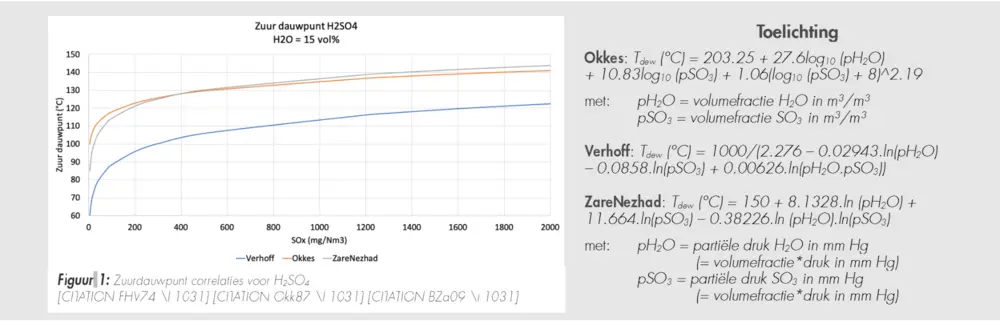
Voordelen polymere warmtewisselaar
Heat Matrix heeft in 2017 de eerste Energy Enlightenmentz-prijs gewonnen met deze polymere warmtewisselaar. Deze innovatieve technologie maakt warmteterugwinning uit corrosieve of vervuilende rook- en uitlaatgassen mogelijk. Deze warmte kan gebruikt worden voor het voorverwarmen van verbrandingslucht of een waterstroom en daarmee de algehele energie-efficiëntie significant verhogen. Implementatie op een site kan leiden tot een verhoging van de totale energie-efficiëntie tot 5% op fornuizen [CITATION Swa19 \l 1033] en tot 25% op drogers (dit getal is gebaseerd op eigen ervaring van HeatMatrix: drogers opereren normaliter rond de 200-250 °C. Met deze technologie kan ca. 60-70 °C kostenefficiënt worden voorverwarmd, wat neerkomt op een besparing van ongeveer 25%). Door het rookgas in de polymere warmtewisselaar door het zuurdauwpunt (Engels: Acid Dew Point – ADP) heen te koelen wordt zuur gecondenseerd en de corrosiviteit van het rookgas gereduceerd.
De HeatMatrix APH (Air PreHeater) of LUVO (luchtvoorverwarmer) is gebaseerd op Polymer Honeycomb technologie. In deze technologie worden meerdere buizen met elkaar verbonden, die samen een modulaire bundel (Figuur 2) vormen. De corrosiebestendige polymeren bundels worden gemonteerd in een metalen behuizing (Figuur 2) om het benodigde warmte-uitwisselend oppervlak te creëren.
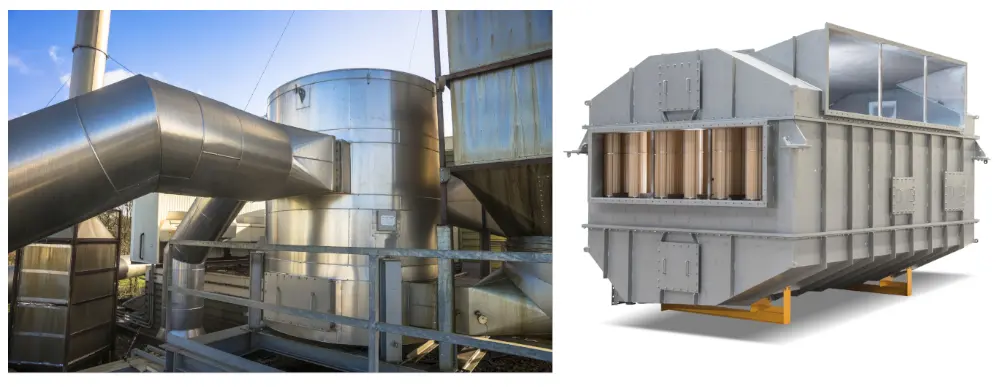
De Polymer Honeycomb-technologie zorgt voor een robuuste warmte-uitwisselingsmatrix die bestand is tegen hoge gassnelheden en thermische schokken. De geometrie creëert een 100%-tegenstroomconfiguratie tussen het rookgas en de luchtstromen. Het rookgas stroomt van boven naar onder door de buizen (Figuur 2, de rode pijl) en de verbrandingslucht stroomt in tegengestelde richting om de buizen heen (Figuur 2, blauwe pijl). Binnen de polymeren buizen wordt het rookgas door het zuur dauwpunt heen gekoeld en condenseert er zwavelzuur op buiswand. In de onderste sectie, wordt het condensaat van het rookgas gescheiden, afgevangen en afgevoerd.
Naast corrosiebestendigheid biedt polymeer ook voordelen in vervuilende condities. Polymeren hebben een glad oppervlak en een lage affiniteit voor bindingen met stof, roet, zouten en andere kleine deeltjes. Bovendien zijn de bundels verticaal gemonteerd en is er door de condensatie in de bundels een mild reinigend effect. Dit vertraagt de opbouw van vervuiling. In gevallen van extreem vervuilende rookgassen, kunnen de bundels gereinigd worden middels een ingebouwd sproeisysteem.
Vergelijkbare polymeertechnologie wordt ook toegepast in de HeatMatrix ECO. In deze wisselaar kan met de restwarmte van het rookgas voedingswater voor boilers en WKK’s, proceswater en reinigingswater worden verwarmd. Tevens kan de warmteterugwinning worden ingezet voor een extern warmtenet. Dit zorgt ervoor dat er verder gekeken kan worden dan alleen naar de interne energiebehoefte.
Wat gebeurt er downstream?
De eerdergenoemde condensatie van zwavelzuur in de wisselaar betekent dat SO3 selectief verwijderd wordt uit het rookgas. Dit heeft als bijkomend voordeel dat het zuur dauwpunt verlaagd wordt en het rookgas direct minder corrosief wordt.
Om dit te staven, is er een onderzoek uitgevoerd in samenwerking met TNO naar het effect binnen de HeatMatrix Air PreHeater. Gedurende het testprogramma is een representatief rookgas met SO3 door de polymeren buizen geleid en de SO3-afname over de buizen bepaald. De testresultaten lieten zien dat 80-90% van de SO3 verwijderd wordt in de HeatMatrix Polymer Honeycomb technologie. De condensatie van SO3 resulteert in een zuur dauwpunt daling van 11-15 °C (Figuur 4).
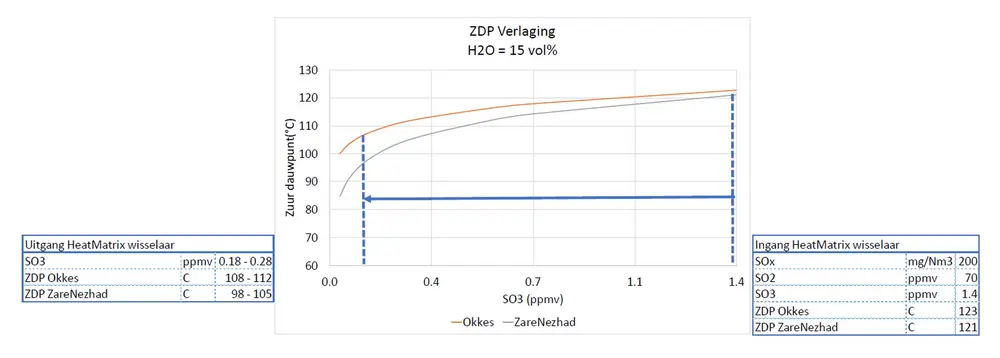
In een praktijktest is bij een van de operationele installaties een koolstofstaal-corrosiecoupon in de uitgang van de HeatMatrix APH geplaatst. De SOx concentratie in het rookgas van deze unit bedroeg 500 mg/Nm³. Analyse na een jaar in operatie bevestigt dat het zuurdauwpunt van het rookgas bij de uitgang van de HeatMatrix luchtvoorverwarmer dermate gedaald is dat de corrosiesnelheid downstream van de LUVO ver onder de typische ontwerp corrosiesnelheid van 0.1 mm/jaar blijft.