Lagers houden machinepark in beweging
Periodieke evaluatie onderhoudsprogramma essentieel
De rol van lagers is dermate cruciaal dat het vroegtijdig onderkennen van problemen een must is. Omdat lagers blootstaan aan allerlei vormen van belasting kan dit niet 'hapsnap', maar dient daaraan een gedegen onderhoudsprogramma ten grondslag te liggen met protocollen voor zaken als (visuele) inspectie, smering en registratie van de lagerprestaties. Periodieke evaluatie van een dergelijk programma en het tijdig doorvoeren van aanpassingen draagt ertoe bij dat de lagers optimaal functioneren, en dat ook blijven doen.
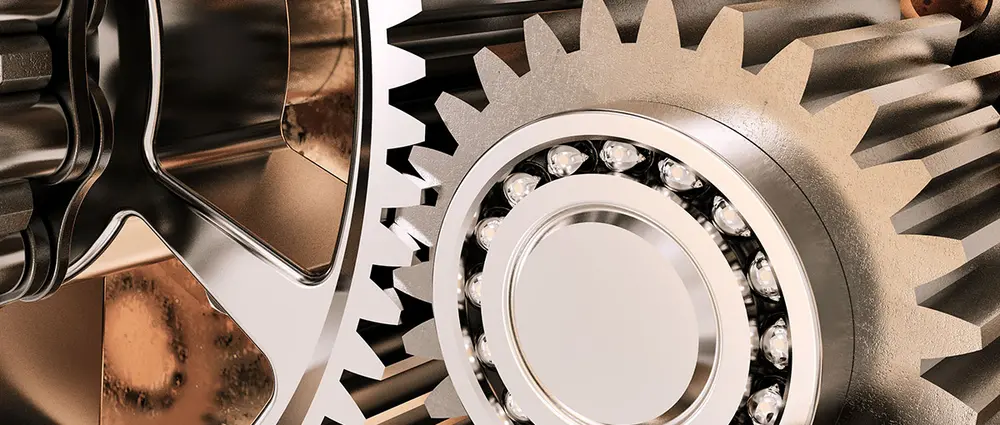
SPILFUNCTIE
Lagers laten roterende en lineaire bewegingen sneller en efficiënter verlopen, voornamelijk door opvang van uiteenlopende hoeveelheden druk, wat de wrijving beperkt. Doorgaans bestaan ze uit:
- een tweetal ringen met daarin de lagerloopbanen: de ene is bevestigd aan het stilstaande constructiedeel, de andere aan het bewegende deel;
- rollende delen – kogels, rollen, kegels of naalden – voor de beweegbaarheid van de ringen ten opzichte van elkaar bij een minimale wrijving;
- een kooi voor de geleiding en het scheiden van de rollende delen.
Een specifiek coderingssysteem ontleend aan diverse internationale normen zorgt er tegenwoordig voor dat lagers met hetzelfde typenummer volledig uitwisselbaar zijn, ongeacht het merk.
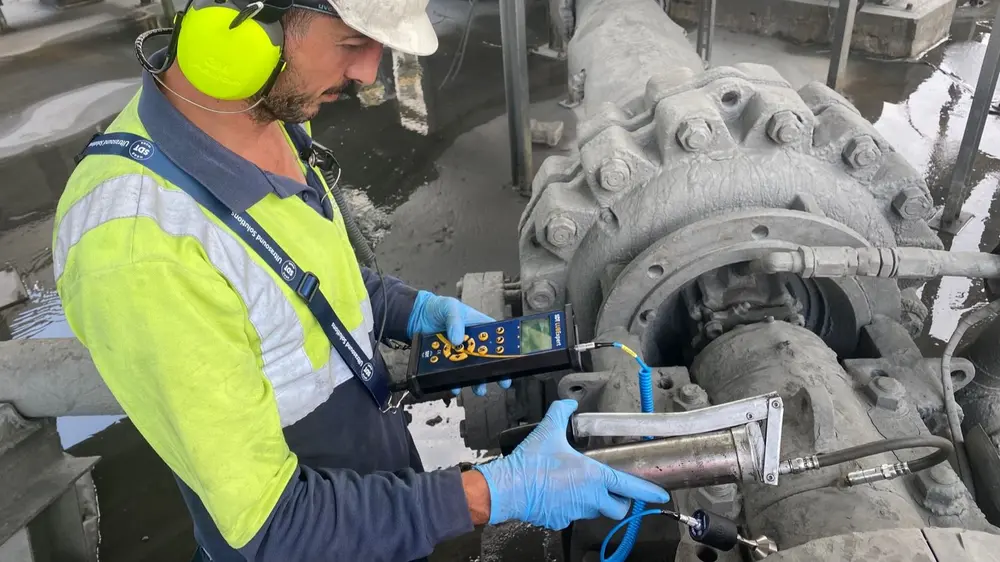
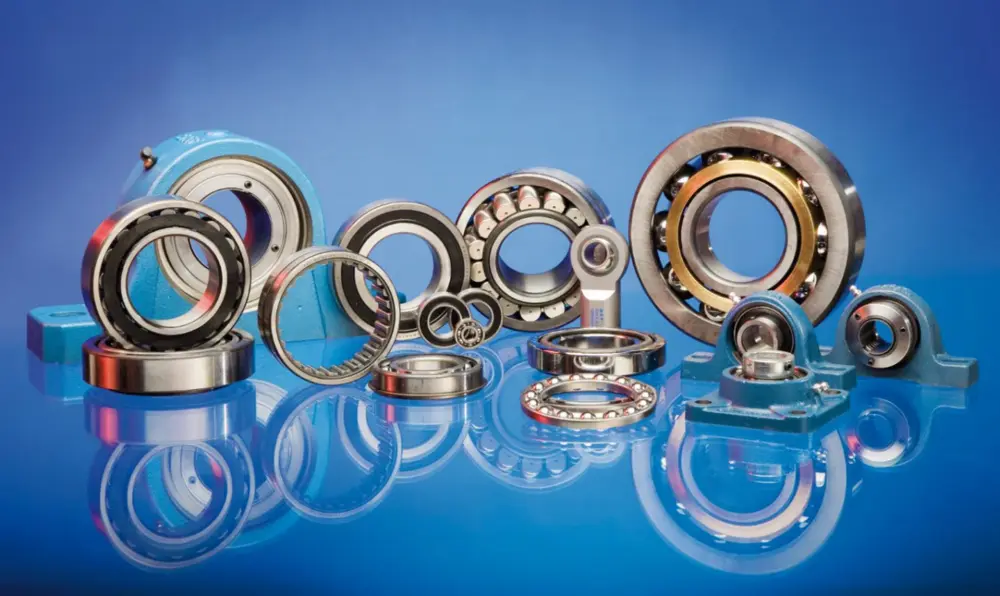
PRESTATIEBEÏNVLOEDENDE FACTOREN
Lagers zijn continu aan belasting onderhevig, wat kan leiden tot allerlei vormen van beschadiging. De norm ISO 15243 beschrijft deze beschadigingen en hun oorzaken.
Mechanische belasting
Doorgaans gaat het daarbij om een combinatie van radiale (haaks op de as) en axiale belasting (in de lengterichting). Daarnaast is er sprake van statische belasting – het lager staat stil en de lagerringen bewegen niet ten opzichte van elkaar – dan wel dynamische belasting waarbij de lagerringen ten opzichte van elkaar draaien (komt het meest voor).
Lagerstoringen gaan ten koste van de veiligheid, de energie-efficiëntie en de productkwaliteit
Om inzicht te krijgen in de mate van belasting is het zaak het prototype hierop te testen. Aandachtspunten daarbij zijn, behalve het lagertype, onder meer de materiaalkeuze, de speling en de toleranties, het ontwerp van de kooi en de afwerking van het oppervlak van de lagercomponenten.
Thermische belasting
De effecten hiervan zijn:
- uitzetting dan wel samentrekking: de opgetreden spanning kan op den duur gevolgen hebben voor onder meer de uitlijning van de lagers en die van de aangrenzende componenten;
- vervorming: herhaalde thermische cycli kunnen leiden tot materiaalmoeheid met mogelijk scheuren en/of schilfering (flaking) tot gevolg.
Een thermische analyse geeft inzicht in de temperatuurinvloeden (zie hierna). Factoren waarmee al tijdens het ontwerp rekening dient te worden gehouden, zijn onder meer de materiaalkeuze, de mogelijkheid tot (externe) koeling en de wijze van afdichting en thermische isolatie.
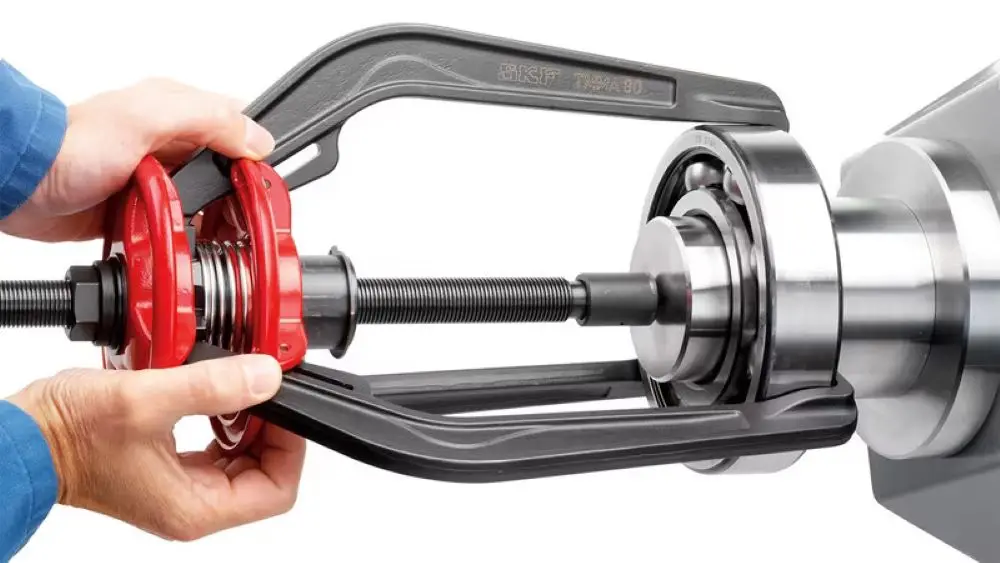
Verontreiniging
Verontreiniging – stof, vuil, corrosieve deeltjes en/of water – kan onder meer aanleiding geven tot slijtage, een verhoogde wrijvingsweerstand, onbalans en trillingen. Afdichtingen beschermen hiertegen. De twee meest gebruikte zijn:
- de 2Z-afdichting: een niet-slepende afdichting bestaande uit een dun stalen afdekplaatje dat verder niet in contact komt met de binnenring. Dit type is bijzonder geschikt voor hoge toerentallen en bij gebruik in omgevingen met hoge(re) temperaturen;
- de 2RS-afdichting: een slepende afdichting bestaande uit een met rubber bekleed staalplaatje waarbij het rubberlipje sleept in een groef op de binnenring met wrijving als gevolg. Dit type wordt gebruikt bij matige verontreiniging of wanneer een 'spatwater afgedicht' lager een vereiste is.
Vormen van slijtage
• Abrasieve slijtage treedt op wanneer harde(re) deeltjes tussen de lageroppervlakken komen.
• Adhesieve slijtage ontstaat doordat door wrijving tussen de lageroppervlakken microscopisch kleine lasverbindingen ontstaan. Als die vervolgens breken, raken kleine stukjes materiaal los van het oppervlak.
• Corrosieve slijtage is het gevolg van chemische reacties tussen lagermateriaal en agressieve omgevingsfactoren met ruwheid/oppervlakteverlies tot gevolg.
• Elektrische slijtage treedt op wanneer sprake is van elektrische ontladingen tussen lageroppervlakken, bijvoorbeeld bij hogesnelheidsrotaties. Microscopisch kleine putjes in het oppervlak zijn het gevolg.
• Erosieve slijtage wordt veroorzaakt door de impact van kleine harde deeltjes, bijvoorbeeld zand.
• Vermoeiingsslijtage ontstaat door herhaalde ontlading en belasting, gevolgd door scheurtjes en uiteindelijk het loslaten van partikeltjes.
• Wrijvingsslijtage treedt op wanneer bij onvoldoende smering de wrijvingskrachten tussen de lageroppervlakken een druk- en temperatuursverhoging veroorzaken.
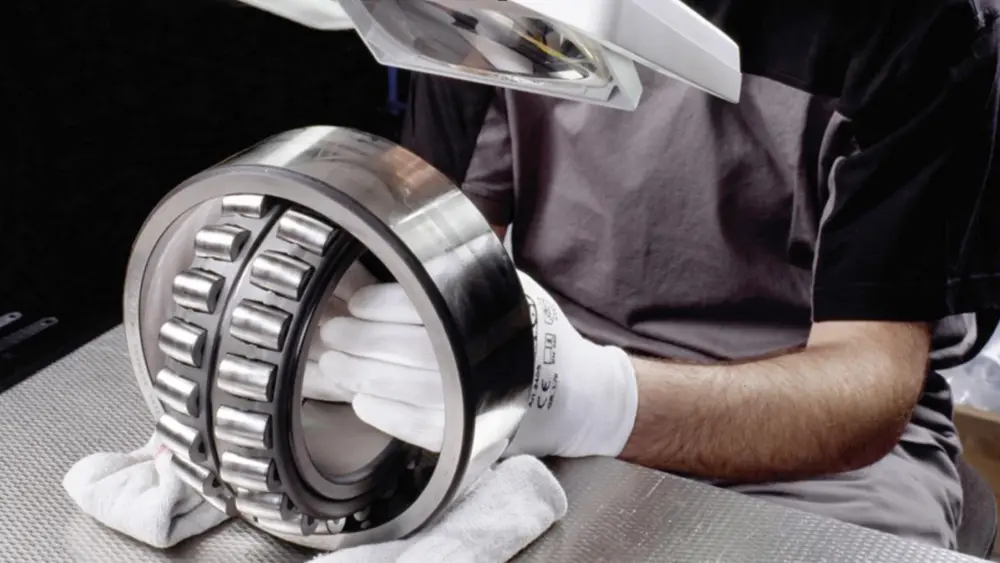
MAINTENANCE
Lagerstoringen gaan ten koste van de veiligheid (van personeel én installatie), de energie-efficiëntie (meer wrijving en dus energieverlies) en de productkwaliteit. Bovendien kunnen slecht functionerende lagers stilstand veroorzaken, een aanzienlijke kostenpost ook al omdat de vervanging ervan een tijdrovende aangelegenheid is.
Inspectie
Door lagers regelmatig aan een inspectie te onderwerpen (condition monitoring) kunnen problemen worden gedetecteerd en onderkend, nog voor ze tot ernstige schade of uitval leiden. Voorbeelden daarvan zijn trillings-, temperatuur- en ultrasone analyse.
Trillingsanalyse
Afwijkende trillingspatronen kunnen uiteenlopende oorzaken hebben variërend van montagefouten, onjuiste uitlijning en smeringsproblemen tot corrosie, overbelasting en slijtage (zie kader). Voor trillingsanalyse gebruikte controletechnieken zijn onder meer:
- frequentieanalyse, gebaseerd op het feit dat lagers trillingen genereren op specifieke frequenties, onder meer afhankelijk van factoren als rotatiesnelheid en het aantal lagerrollen. Afwijkende frequenties kunnen duiden op problemen;
- online monitoring, waarbij dankzij op de lagers aanwezige sensoren realtimegegevens beschikbaar zijn over hun functioneren;
- spectraalanalyse, waarbij de trillingsamplitude een functie is van de frequentie. Sommige piekwaarden in het spectrum zijn karakteristiek voor bepaalde problemen.
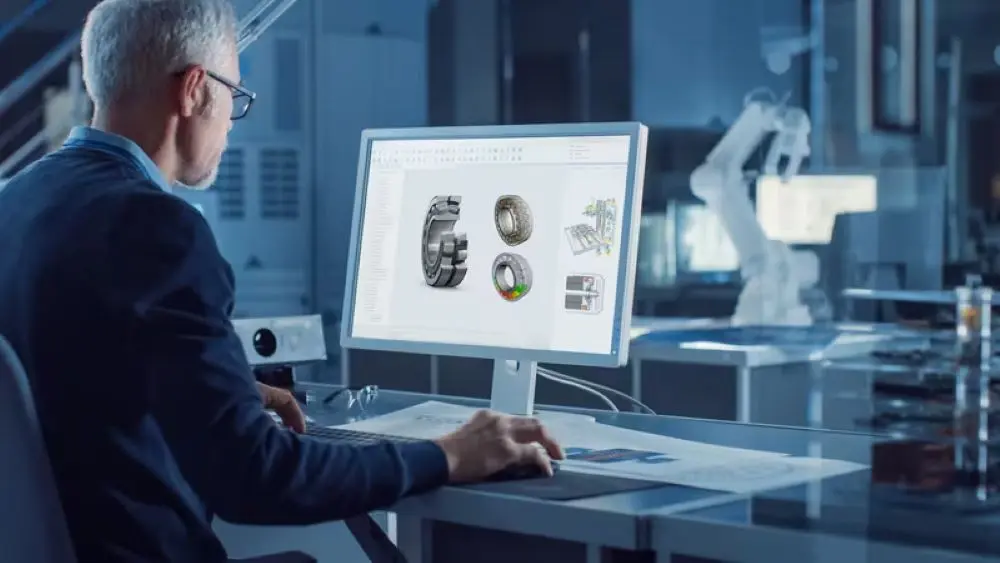
Temperatuuranalyse
De karakteristieke bedrijfstemperatuur van lagers wordt bepaald door factoren als belasting, snelheid en smering; temperatuurafwijkingen treden doorgaans al op voordat andere symptomen manifest worden (signaalfunctie). Een (te) hoge temperatuur kan overmatige wrijving veroorzaken en/of ervoor zorgen dat het smeermiddel desintegreert. Controletechnieken zijn onder meer:
- het controleren van temperatuurgradaties aan het lageroppervlak: verstoring daarvan kan duiden op ongelijkmatige smering of overmatige belasting van een bepaald deel van het lager;
- online monitoring: ook hier zorgt de aanwezigheid van sensoren op de lagers voor real-time informatie.
Bij automatische systemen wordt een alarm afgegeven zodra de temperatuur een vooraf ingestelde grenswaarde overschrijdt.
Ultrasone analyse
Lagers genereren geluidsgolven die kunnen worden beluisterd met behulp van ultrasone instrumenten, ook wel ultrasone vertalers genoemd. Wanneer de frictie in het lager toeneemt, dan neemt ook het niveau van de gegenereerde ultrasone golven toe; een wijziging in het decibelniveau is het gevolg. Wordt dit hoger, dan duidt dit op een hogere mate van frictie, bijvoorbeeld door wrijving, slijtage, scheuren, gebrek aan smering en/of de aanwezigheid van oneigenlijke voorwerpen.
Problemen kunnen op die manier worden gedetecteerd al voordat er daadwerkelijk storingen optreden en – ook niet onbelangrijk – terwijl de apparatuur in bedrijf is.
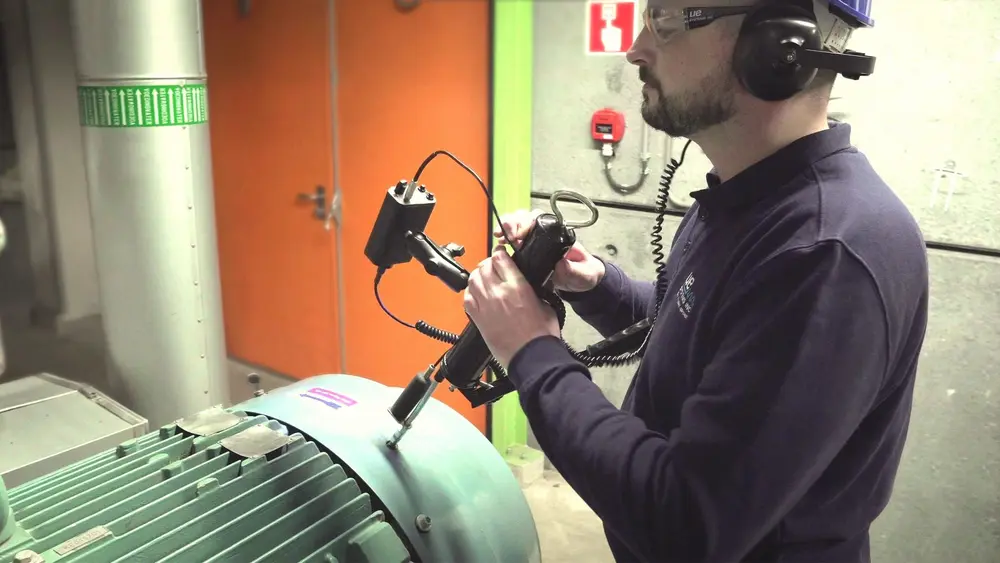
Smering
Het primaire doel hiervan is beperking van slijtage als gevolg van wrijving. Daarnaast stimuleert het de warmteafvoer, bevordert het de afdichtende werking en gaat het verontreinigingen tegen. Smering vindt doorgaans plaats met behulp van vet – olie is te dun – bestaande uit oliën, een verdikker en additieven. Een effectieve afdichting maakt dat het smeermiddel binnen en de verontreinigingen buiten blijft. Standaard afgedichte lagers zijn al van vet voorzien (circa 30% van de vrije ruimte).
Een correcte (de)montage voorkomt schade en is mede bepalend voor de levensduur
Bepalend voor de smeermiddelkeuze zijn de belasting, de omgevingsomstandigheden (bijvoorbeeld de heersende druk en/of temperatuur), de bewegingssnelheid en eigenschappen als waterbestendigheid en temperatuurbereik (de verdampingssnelheid van het middel bepaalt voor welke temperaturen het geschikt is).
Montage- en demontagetechnieken
Een correcte (de)montage voorkomt schade en is mede bepalend voor de levensduur.
Tips voor montage
- lager en behuizing moeten passend zijn, anders treedt er direct beschadiging op;
- verwarm de lagers vooraf enigszins;
- bij montage in een warme omgeving het lager vooraf koelen;
- tijdens de montage geleidelijk en gelijkmatig druk uitoefenen;
- gebruik een geschikte pers en een lagermontageset.
Tips voor demontage
- verwarm de omringende metalen componenten enigszins: uitzetting daarvan vergemakkelijkt het verwijderen;
- maak gebruik van een lagerafnemer (trekker) of pers;
- vermijd scherpe gereedschappen;
- gebruik bij corrosie roestoplossende sprays of penetrerende oliën;
- tik bij vastloop, zonder te forceren, met een zachte hamer op de buitenring.
Het is zaak bij de montage en de demontage te werken volgen de fabrieksinstructies en bij problemen professionele hulp in te schakelen.
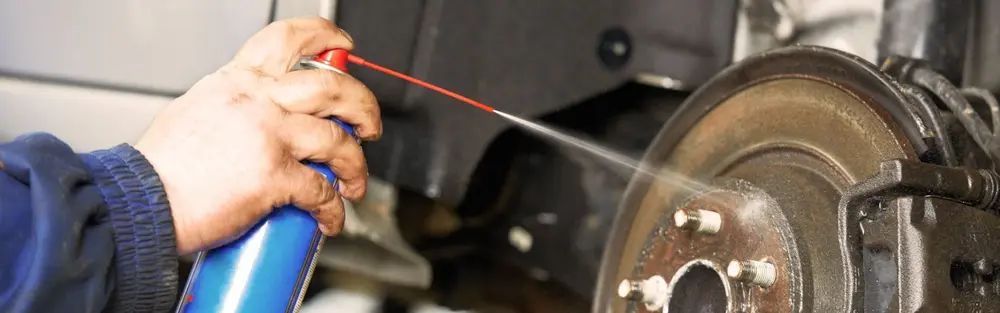
ONDERHOUDSPROGRAMMA
Een gedegen onderhoudsprogramma is geen overbodige luxe. Het vergemakkelijkt vroegtijdige onderkenning van problemen en voorkomt mede daardoor schade of uitval, op voorwaarde dat het onderhoudspersoneel daartoe voldoende is opgeleid/getraind en geëquipeerd.
Een onderhoudsprogramma moet in ieder geval protocollen bevatten voor:
- de diverse vormen van inspectie (zie het betreffende item);
- toereikende smering (frequentie, type smeermiddel en hoeveelheden);
- het bijhouden van de lagerprestaties;
- het toegankelijk vastleggen van de onderhoudsactiviteiten;
- de wijze van opslag van de reserve-onderdelen;
- uitlijning en balancering van (de onderdelen van) machines.
Uiteraard dient er sprake te zijn van een periodieke evaluatie van het onderhoudsprogramma en het op basis daarvan doorvoeren van noodzakelijke aanpassingen.
Met medewerking van ERIKS, Schaeffler, SKF en UE Systems