Carrosserie Karreveld: une entreprise familiale à l'échelle industrielle
"Il faut sortir de sa zone de confort, sinon on recule"
Cela fait maintenant 17 ans que la Carrosserie Karreveld est installée à Machelen. L'entreprise des trois frères Bytyci continue de croître grâce à des investissements réguliers dans la technologie. Ainsi, l'entreprise a récemment acheté la machine de dosage Irus Mix d'Axalta, qui permet de mélanger la bonne quantité de peinture et de gagner du temps. Un routage astucieux dans l'atelier, des employés bien formés et une bonne infrastructure font en sorte qu'un client ne manque sa voiture qu'au maximum trois à quatre jours ouvrables.
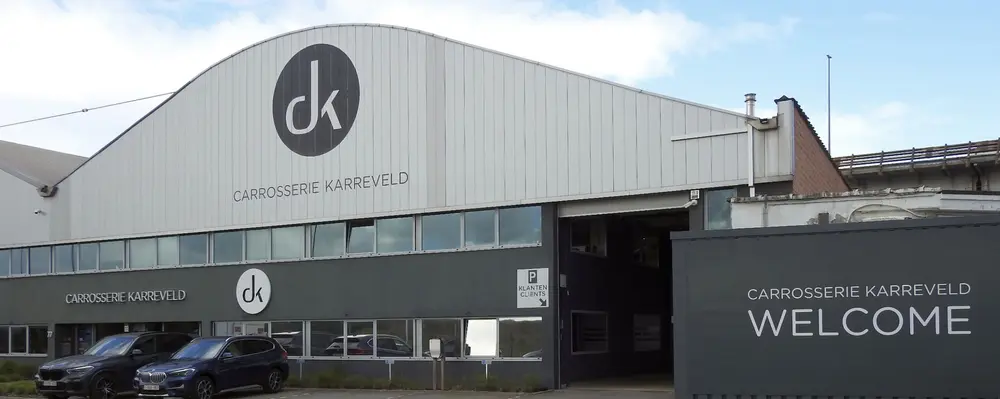
Trois frères toujours présents
De trois carrosseries à une seule
Nous avons visité la Carrosserie Karreveld, située sous le "viaduc de Vilvorde" à Machelen. Avant que les trois frères Bytyci ne s'y installent dans un nouveau bâtiment (2007), ils disposaient de trois carrosseries disséminées dans Bruxelles. Ce sont leur oncle et sa sœur, leur mère, qui ont ouvert la première en 1970. Leur père, arrivé plus tard, a rejoint le duo. Les "trois mousquetaires", comme on appelle parfois les frères, ont également rejoint l’affaire et chacun d'eux dirige aujourd'hui l'entreprise à Machelen.
“A condition d'investir et de disposer d'une structure organisationnelle optimale, le travail viendra à vous en un rien de temps”
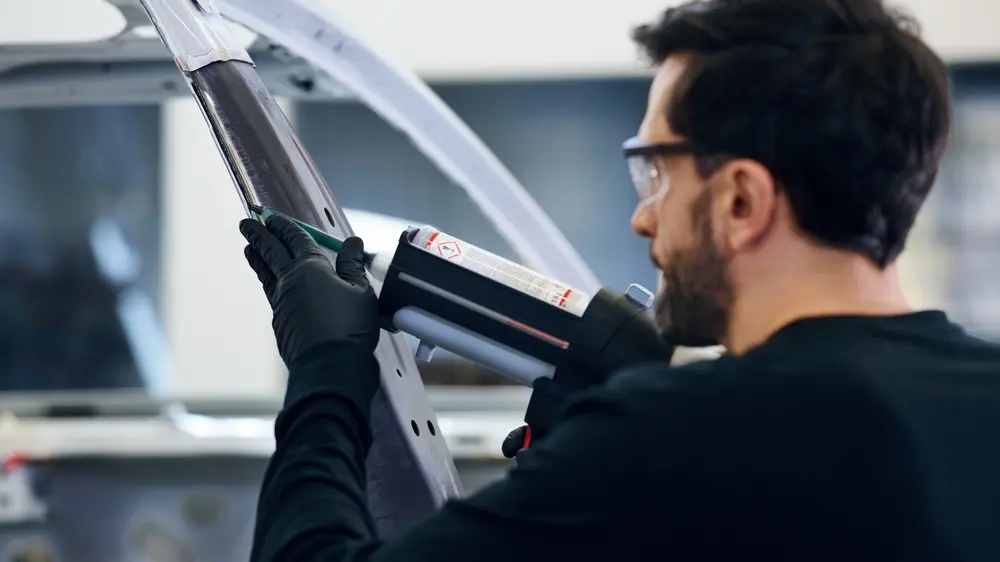
170 réparations par semaine
Nous nous sommes entretenus avec Faton Bytyci, PDG de la Carrosserie Karreveld: "La décision de remplacer les trois ateliers de carrosserie par une seule carrosserie s'est avérée judicieuse. Nous effectuons ici beaucoup plus de réparations qu'auparavant sur les trois sites réunis (170 par semaine contre 150 dans les trois sites réunis), et nous le faisons avec moins de collaborateurs (40 contre presque le triple auparavant). Nous pouvons travailler de manière très efficace sur cet emplacement. Et nous n'avons plus besoin de nous déplacer d'un site à l'autre."
En moyenne 3 à 4 jours
Routage
Depuis le couloir du premier étage, où se trouvent les bureaux, nous avons une bonne vue sur le routage dans le grand atelier. Les voitures à traiter entrent par l'entrée vers les places de parking marquées en bleu. Elles se dirigent rapidement vers la zone de “démontage – tôlerie”, où le véhicule est minutieusement contrôlé.
La voiture passe ensuite dans la zone de "préparation" adjacente, où les parties nécessaires de la voiture sont marouflées pour les protéger pendant les travaux de carrosserie. La voiture passe ensuite dans la zone de "peinture", puis dans la zone de "montage". Ensuite, chaque voiture est soumise à un contrôle final et reçoit l'approbation d'Agron. Avant de quitter l'atelier, chaque voiture est lavée.
Réparation intelligente
"En moyenne, une voiture reste chez nous pendant 3 à 4 jours. Une voiture qui entre pour une réparation intelligente, c'est-à-dire une voiture très légèrement endommagée, par des rayures par exemple, et qui peut être réparée localement, suit un routage légèrement différent et repart en deux jours au maximum", explique Faton. "Dans le cas d'une réparation intelligente, un “smart repair”, nous pouvons minimiser les coûts de réparation. Un smart repair n'est donc pas seulement écologique, mais également économique."
Activités
Travaux de moindre envergure
Chaque jour, Carrosserie Karreveld réceptionne des voitures dont les jantes sont abîmées. Les employés essaient d'abord de les réparer. Nous voyons aussi des voitures qui doivent être polies parce que la carrosserie a été endommagée par de la résine d'arbre, par exemple (lorsqu'elles sont garées sous des arbres). Et certains véhicules ont besoin d'être débosselés sans qu'une nouvelle couche de peinture soit nécessaire par la suite ("PDR").
Mélanger la peinture
La majorité des voitures arrivent suite à un accident et nécessitent une nouvelle couche de peinture après réparation. Après tout, nous sommes dans un atelier de carrosserie. Ax, à l'atelier, nous explique le mélange de la peinture.
"Pendant longtemps, nous devions nous contenter des échantillons de couleur des marques automobiles et deviner la bonne couleur. (Nous les voyons encore pendre comme des souvenirs dans une armoire du laboratoire de peinture, ndlr). Plus tard, le scanner qui détermine précisément la composition de la peinture a fait son apparition sur le marché. Un employé prenait alors les bons pots, pesait des quantités précises et commençait à mélanger. Cependant, il restait toujours de la peinture inutilisable. Quel 'gâchis'!”
Irus Mix
"Heureusement, une machine est apparue sur le marché qui rend le mélange manuel superflu. Depuis février 2024, nous disposons d'une Irus Mix (de la société Axalta, ndlr). C'était la machine qu'il nous fallait", explique Ax avec enthousiasme. "L'ouvrier n'a plus qu'à entrer les données obtenues par le scanning. Puisqu'un robot fabrique la peinture et choisit les quantités exactes, nous n'avons plus de surplus."
"De plus, cela libère du temps pour l'ouvrier, qui peut effectuer d'autres tâches dans l'intervalle. Pour vous donner une idée: pour une réparation intelligente, nous devions auparavant utiliser 250 g de peinture, aujourd'hui il ne nous en faut plus que 40 g."
"Pour une réparation intelligente, nous devions auparavant utiliser 250 g de peinture, aujourd'hui nous n'en utilisons que 40 g avec l'Irus Mix"
Investissements
"Nous pensons qu'il est très important de réaliser des investissements, surtout s'ils nous aident à travailler de manière plus durable. D'ailleurs, il y a quelques années, nous avons obtenu le label Long Life Repair", explique Agron alors que nous nous promenons dans l'atelier.
"L'Axalta Irus Mix a coûté 40.000 euros, la station de lavage écologique 60.000 euros, le fly dry (qui sèche les parties de la carrosserie avant de les peindre, ndlr) 600.000 euros et le nouveau pont de géométrie 65.000 euros. Nous avons investi 250.000 euros dans les panneaux solaires. Grâce à toutes ces techniques modernes, nous sommes extrêmement performants.”
80% d'entreprises comme clients
La situation géographique de la Carrosserie Karreveld (à proximité des zones d'activités de Diegem, Zaventem, Brussels Airport ...) explique à elle seule pourquoi la majeure partie des personnes qui s'y rendent avec leur voiture sont des employés d'entreprises disposant d'une voiture en leasing (80%). 20% sont des clients privés dont l'assurance les oriente vers la Carrosserie Karreveld. L'entreprise répare toutes les marques de véhicules jusqu'à 3,5 tonnes.
Des chauffeurs viennent chercher les voitures
Pas moins de trois chauffeurs récupèrent les véhicules chez les clients finaux tout au long de la journée. Quatre-vingts voitures de remplacement/fourgonnettes sont disponibles. Si quelqu'un préfère repartir en vélo électrique, c'est également possible. Si nécessaire, la Carrosserie Karreveld se rend sur place pour laver les véhicules utilitaires à la vapeur. Quoi qu'il en soit, les frères sont ouverts à tout. "Si une entreprise cliente demande quelque chose, elle l'obtient", affirment-ils.
Familial et industriel
Plus de 40 collaborateurs
Avec combien de collaborateurs la Carrosserie Karreveld réalise-t-elle tout cela? "Plus de quarante, y compris nous-mêmes. Une dizaine de collaborateurs s'occupent de la réception, du département comptabilité et du département marketing. Près de 30 personnes travaillent à l'atelier, une personne est constamment sur la route pour débosseler les petites bosses sur place et, comme évoqué plus haut, trois chauffeurs sillonnent les routes en permanence."
Horaires de travail variables
"Nous sommes toujours tous les trois dans l'atelier, il n'y a pas d'autres chefs ou patrons", confie Faton avec le sourire. "Nous veillons à ce que nos collaborateurs se sentent bien au travail et nous leur accordons des horaires variables, par exemple pour qu'ils puissent encore emmener leurs enfants à l'école avant de commencer à travailler ici. Nous sommes proches d'eux et les traitons comme des membres de la famille."
"En fait, nous sommes une entreprise familiale à l'échelle industrielle. À intervalles réguliers, nous faisons quelque chose d'extra pour nos employés, par exemple en louant un food truck de pizzas. Nos employés choisissent eux-mêmes leurs périodes de congé, car nous sommes ouverts toute l'année. En juillet et en août, les effectifs peuvent de toute façon être réduits parce que le travail diminue un peu à ce moment-là. Nous adaptons alors les rotations nécessaires dans les horaires de travail."
Chacun suit des formations
Chaque employé suit une formation deux fois par an afin de rester à jour. "Car, tout comme un téléphone portable, un employé a besoin d'une mise à jour", explique Faton. Le centre de formation spécialisé dans le secteur automobile Educam est leur partenaire.
Il se rend sur place pour dispenser des formations en petits groupes. Celles-ci peuvent porter sur les propriétés d'une carrosserie en aluminium, par exemple, ou sur les tests de diagnostic. Quelques ouvriers ont obtenu un certificat attestant de leur expertise dans le domaine des véhicules électriques.
"Mes frères et moi, nous nous tenons également au courant à travers des formations et des séminaires. Nous devons constamment apprendre de nouvelles choses et oser sortir de notre zone de confort, sinon nous régressons. C'est notamment parce que je suis membre de la fédération des carrossiers Febelcar et du label de qualité et du fonds de garantie Eurogarant que je sais vraiment ce qui se passe dans ce petit monde", poursuit Faton.
Avancer grâce à la technologie
Remplacer les pièces plus rapidement
À notre question de savoir si, grâce aux nouvelles technologies que les voitures utilisent aujourd'hui, il y a moins d'accidents qu'auparavant, Faton répond que c'est effectivement le cas. Mais les réparations après un accident sont plus importantes aujourd'hui. Une autre grande différence par rapport à celle d'il y a 20 ans est que les pièces sont remplacées plus rapidement, car l'aluminium n'est pas aussi résistant que l'acier. L'acier était plutôt réparé que remplacé.
Le travail manuel restera nécessaire
Et comment voit-il l'avenir? "À mon avis, les carrosseries qui ne vont pas très bien aujourd'hui sont celles qui ne sont pas bien équipées. Il faut oser prendre des risques, investir dans les nouvelles technologies qui permettent de fournir une qualité supérieure, sinon on ne progresse pas. Grâce aux investissements et à une structure organisationnelle optimale, le travail vient à vous."
"Notre ambition est de continuer à croître, année après année. Pour réussir, nous devons pouvoir convaincre les jeunes de la beauté du métier de carrossier. C'est un artisanat. Le travail manuel restera toujours nécessaire, même si la numérisation et l'automatisation ont pénétré dans notre secteur", conclut le PDG de la Carrosserie Karreveld..
Cinq points forts de Carrosserie Karreveld
1. Les personnes qui n'ont pas besoin d'un véhicule de remplacement sont les bienvenues sans rendez-vous.
2. Une qualité élevée, en partie grâce à des investissements dans la technologie.
3. Chaque employé reçoit une formation deux fois par an.
4. Trois chauffeurs récupèrent et ramènent les voitures.
5. Ouvert toute l'année