Le système de lubrification communique via un réseau Mesh
La maintenance prédictive fait son chemin dans les nouveaux produits
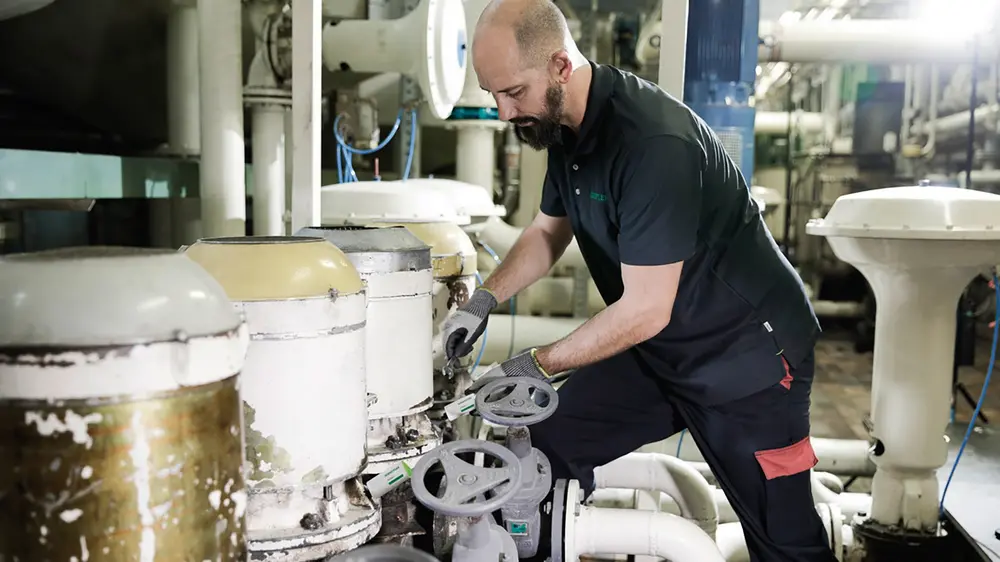
Dans le cadre des "Lifetime Solutions", Schaeffler a introduit dans le programme OPTIME un système de lubrification automatique qui communique via ce qu'on appelle un réseau Mesh: OPTIME C1. Le département de maintenance est ainsi informé automatiquement du fonctionnement du système de lubrification et de la quantité de graisse restante. Les tournées d'inspection appartiennent donc au passé et le risque de dysfonctionnement dû à des systèmes de lubrification vides est considérablement réduit.
Lubrifier, mais pas inspecter
Les systèmes de lubrification automatique ne sont pas nouveaux. Depuis des années, ils sont utilisés comme alternative à la lubrification manuelle qui permet de gagner du temps. Toutefois, des tournées d'inspection restent nécessaires pour vérifier si les systèmes doivent être remplis et si tout fonctionne comme il se doit.
Schaeffler, fabricant de longue date de roulements tels que INA et FAG, notamment, a mis au point une solution qui permet également de minimiser le nombre de tournées d'inspection: l'OPTIME C1. Il s'agit d'un système de lubrification automatique qui fonctionne sur batterie et communique sans fil tant sur son fonctionnement que sur son contenu. La communication s'effectue via ce qu'on appelle un réseau Mesh.
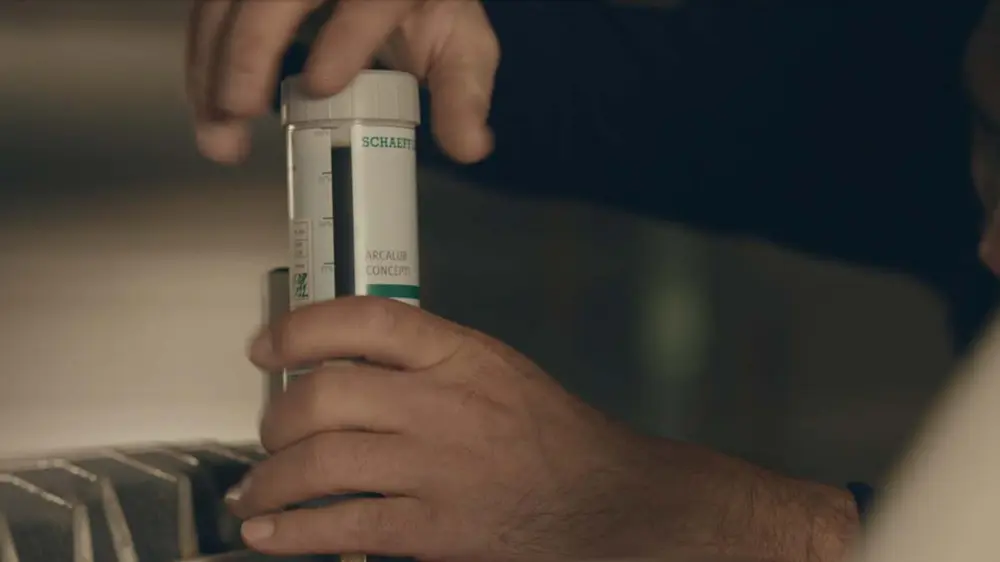
Qu'est-ce qu'un réseau mesh?
Il s'agit en fait d'un réseau 'maillé'. Il se compose de différents nœuds qui sont connectés et communiquent entre eux. Dans le réseau Mesh de Schaeffler, ces nœuds comprennent notamment des capteurs qui enregistrent le fonctionnement et le contenu du système de lubrification automatique. Chaque capteur qui génère des informations les transmet au capteur suivant le plus proche, de sorte que toutes les informations arrivent finalement à une passerelle: un point central qui recueille toutes les données.
Dans la solution OPTIME, la passerelle peut recevoir des informations provenant de 70 capteurs au maximum. Si le réseau comprend un plus grand nombre de capteurs, il est toujours possible d'augmenter le nombre de passerelles.
Avantages
Un tel réseau présente plusieurs avantages. Tout d'abord, la communication est sans fil, ce qui signifie qu'il n'est pas nécessaire de câbler chaque capteur séparément. Par ailleurs, les capteurs ne doivent pas communiquer individuellement avec un point central, mais seulement avec le capteur le plus proche. Cela signifie que la quantité d'énergie nécessaire à la communication des données est minimale. Enfin, un réseau maillé offre l'avantage que la défaillance d'un capteur ou d'un nombre limité de capteurs n'entraîne pas la défaillance de l'ensemble du réseau. Au contraire. En cas de capteur défectueux, il se répare lui-même, en ignorant ces capteurs et en recherchant un nouveau capteur plus proche.
Un exemple schématique est présenté dans la figure ci-dessous.
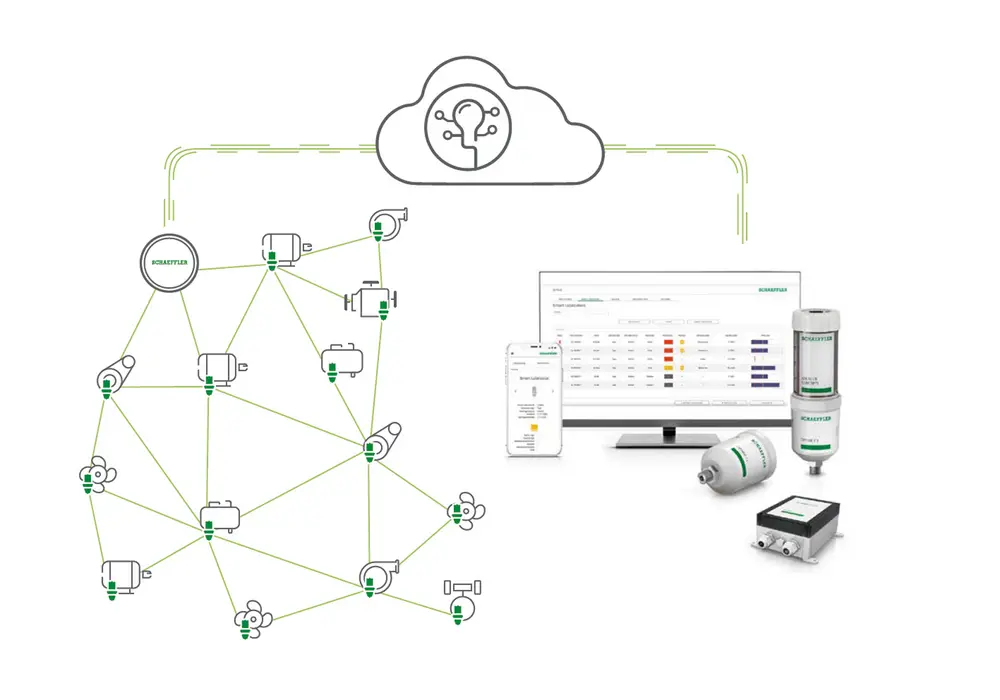
Dennis Fischer est coordinateur de Schaeffler Lifetime Solutions et déclare: "Sur cette figure, non seulement les capteurs des systèmes de lubrification automatique sont visibles, mais vous pouvez également voir d'autres capteurs. Il s'agit des capteurs de vibrations SmartCheck à l'origine du programme OPTIME. Ces capteurs de vibrations relativement simples sont montés sur des roulements, des pompes, des ventilateurs ou des moteurs et communiquent également leurs propres données de vibration à la passerelle centrale via le réseau Mesh. Ces données renseignent sur l'état de l'actif en question et contribuent ainsi à la surveillance conditionnelle ou à la maintenance prédictive."
État et alarmes
Toutes les données qui sont rassemblées en un point central sont automatiquement analysées par le système OPTIME et remontées activement via l'application associée et l'application PC. Ceci signifie que l'utilisateur peut visualiser en ligne l'état actuel des différents actifs et qu'il est averti en temps voulu en cas de dépassement des valeurs prédéfinies. Par exemple, lorsque le lubrifiant vient à manquer ou que le système se bloque ou fuit.
Économiser les coûts
Fischer: "Vous pouvez imaginer que cette méthode de travail permet d'économiser de nombreux coûts. Tout d'abord, toutes les tournées d'inspection pour vérifier les systèmes de lubrification et faire l'appoint, si nécessaire, sont inutiles. Vous ne devez vous y rendre que lorsque le système OPTIME l'indique. C'est un avantage dans la pratique, surtout pour les points difficiles à atteindre. En effet, ces points sont souvent omis lors des inspections parce que cela coûte trop d'efforts, ce qui peut finalement entraîner un manque de lubrification et éventuellement des dysfonctionnements, voire une défaillance de la machine ou de l'installation."
L'utilisateur peut visualiser en ligne l'état actuel des divers actifs
"Par ailleurs, les temps d'arrêt non planifiés des machines dus à des problèmes de lubrification sont largement évitables. En effet, le département de maintenance peut prendre des mesures immédiates lorsque les capteurs déclenchent l'alarme. Cela permet non seulement d'éviter les entretiens non planifiés - qui sont toujours plus coûteux - mais aussi d'augmenter la disponibilité de la machine et donc la productivité."
Historique
Enfin, les données recueillies par tous les capteurs peuvent être utilisées pour constituer un historique. Des tendances utiles peuvent alors en être déduites, comme le temps écoulé entre le moment où le système de lubrification est rempli et celui où il est presque vide. Il est ainsi plus facile de regrouper les recharges des systèmes de lubrification et de les inclure dans la planification de la maintenance. De plus, cela fournit également des informations précieuses lorsque de nouvelles données s'écartent de manière inattendue de la tendance. C'est presque toujours une indication que quelque chose a changé sur ce point précis. Cela peut être intentionnel, parce qu'un système de lubrification a été réinitialisé, par exemple, mais il peut aussi s'agir d'une fuite ou d'un blocage.
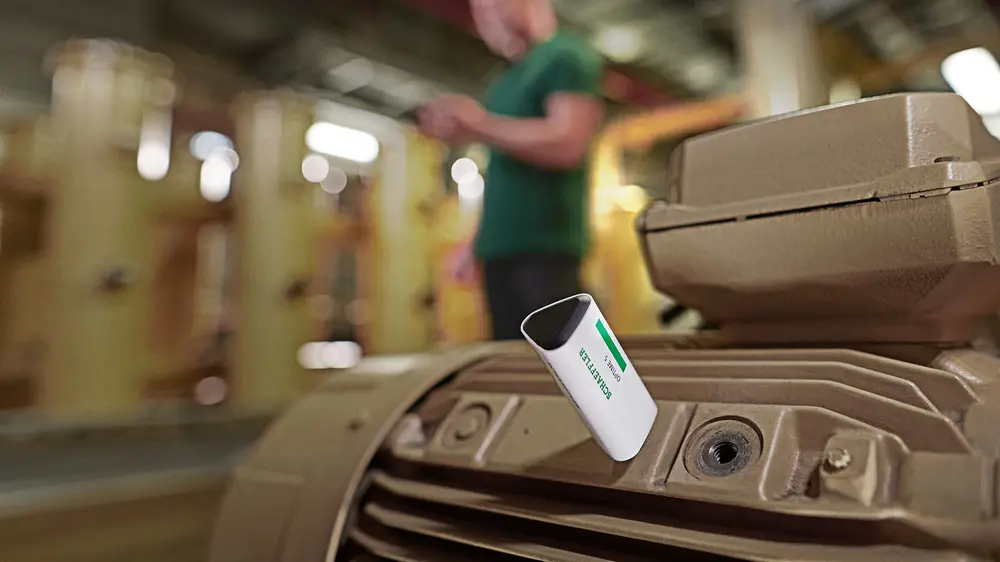
Maintenance prédictive
Avec le lancement d'OPTIME, Schaeffler a concrétisé le thème de la maintenance prédictive.
Fischer: "De nombreuses entreprises sont sans aucun doute conscientes des possibilités et des avantages de la maintenance prédictive et de la maintenance conditionnelle. Leur mise en pratique est toutefois beaucoup plus difficile pour beaucoup. Car par où commencer et que faut-il mesurer ou non?
"Avec OPTIME, nous avons fait un pas vers l'abaissement du seuil de démarrage. Nous y sommes parvenus notamment par la construction modulaire du système. Si vous le souhaitez, commencez par contrôler un seul système de lubrification pour voir ce qu'il fait. Si cela vous donne satisfaction, vous pouvez à tout moment étendre votre propre réseau avec un ou plusieurs dizaines de systèmes de lubrification automatique avec capteurs. Et il en va de même pour les capteurs de vibrations. Commencer simplement et développer les possibilités selon les besoins. Par exemple, commencez par un actif critique et élargissez-le plus tard. Ou commencez d'abord par toutes les pompes dans un local particulier."
Application pour smartphone
En ce qui concerne la convivialité, Schaeffler, pour terminer, a accordé une attention explicite à l'application qui permet de configurer et d'utiliser l'ensemble de l'application.
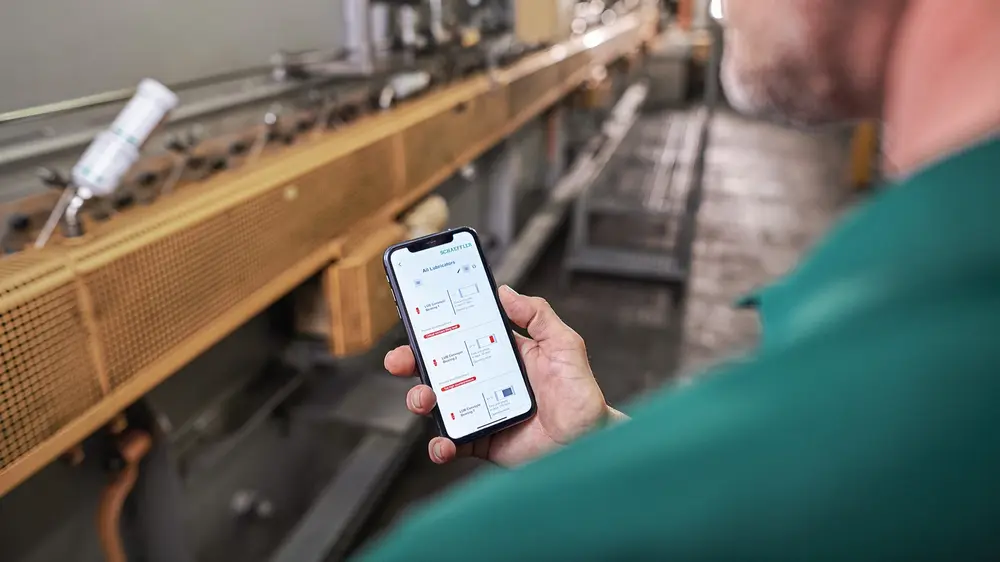
Fischer: "C'est très simple : la technologie peut être belle, mais si l'utilisateur ne la trouve pas facile à utiliser, cette même technologie sera reléguée au second rang en un rien de temps. Nous avons donc développé l'application pour que vous puissiez facilement ajouter un nouveau capteur au réseau en le lisant. Il est tout aussi facile de voir les valeurs mesurées sur un smartphone ou une tablette. En outre, vous pouvez utiliser les paramètres par défaut ou ajuster l'application en fonction de vos besoins et de vos idées."
Avec OPTIME, Schaeffler a établi une base universelle qui peut actuellement être reliée aux capteurs de vibrations et aux capteurs des systèmes de lubrification automatique de l'entreprise. De nouvelles possibilités seront encore ajoutées à l'avenir.